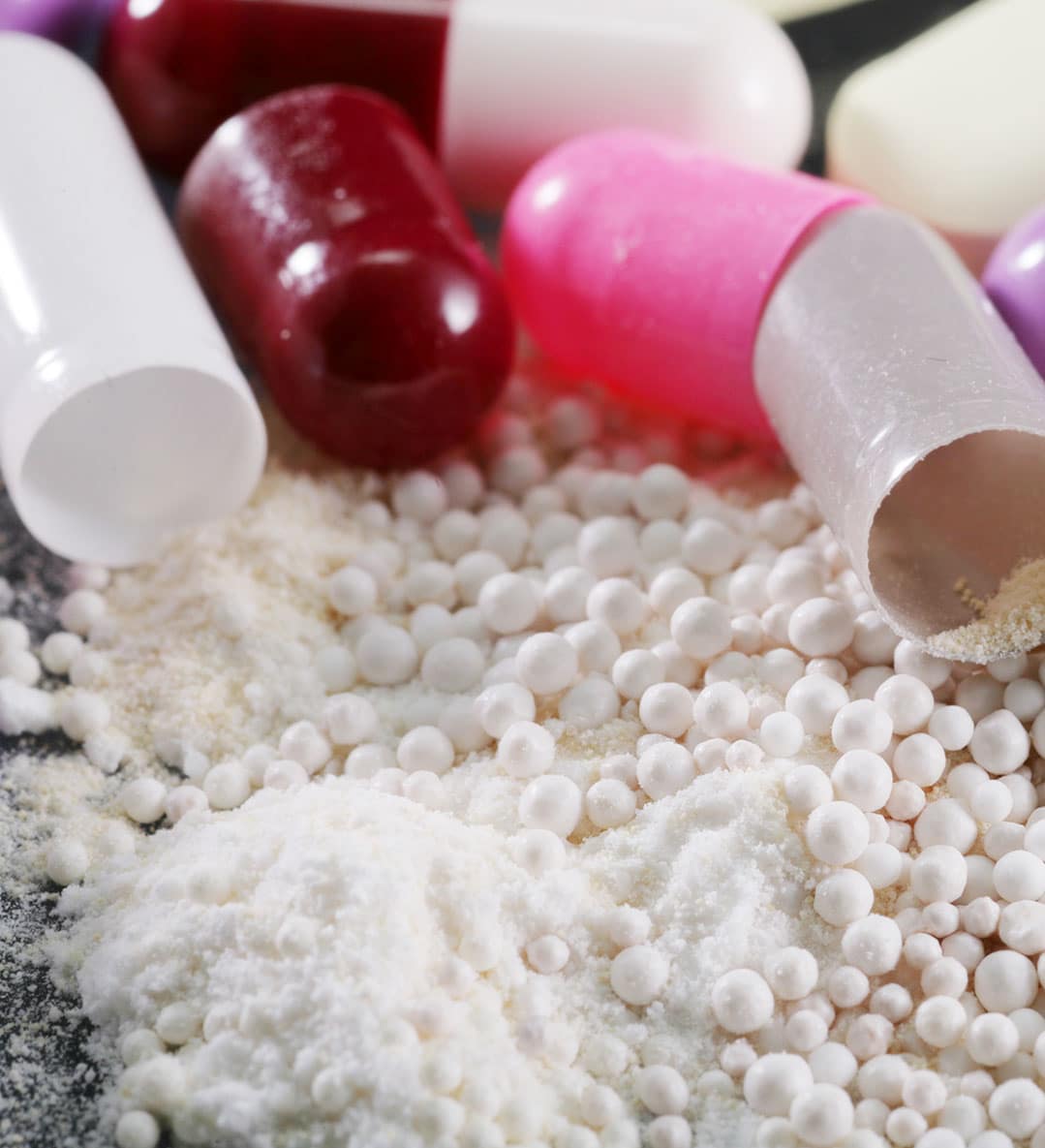
Principles to Powder Mixing the Fast and Easy Way
Powder mixing is common in companies across many industries, including those in the pharmaceutical, advanced materials, and chemical sectors. The powder mixing step is crucial to many processes with the primary objective to achieve uniform distribution of all ingredients. Powder mixing may seem simple, but is often complicated.
Challenges to Powder Mixing
The main challenges with mixing powders are segregation and agglomeration, which are directly related to the flow characteristics and particle sizes of the powders in the mix. Before diving deeper into the problems, it helps to have a basic understanding of powder flow characteristics.
Powder Mixing Characteristics
Powders can be grouped into two main categories based on flow properties:
- Free-flowing - powders that do not cling together.
- Cohesive powders - powders that stick to each other and form aggregates that do not disperse well during mixing.
Several factors influence the formation of aggregates, such as moisture, electrostatic charges, and inter-particle forces.
Additionally, the tendency of powders to be cohesive increases as particle size decreases; in other words, smaller particles tend to be more cohesive while larger particles are more likely to be free-flowing.
How Powder Segregation Occurs
Powder segregation, or demixing, is one of the biggest challenges in powder mixing. Free-flowing powders are at a much higher risk of segregation compared to cohesive mixtures. Segregation typically occurs one of three ways: percolation, vibration, or transportation.
- Percolation occurs when gravity pulls smaller particles into void spaces. This form of segregation typically occurs when powder mixtures have a wider range of particle size.
- Vibration occurs over time as smaller particles are vibrated and shift under larger particles. Similar to percolation, vibration mostly occurs when powders being mixed include large and small particle sizes.
- Transportation occurs as the powder particles are jostled around during transport. In many cases, larger particles segregate to the outside of the container while smaller particles remain closer to the center.
Each of these can occur anytime during the mixing step through transportation and storage of the powdered material.
To combat segregation, companies often minimize the time between the mixing step and the next step in the process, as well as implement special material handling processes.
How Powder Aggregation Occurs
Aggregation is another issue, and often occurs with blending powders in cohesive mixtures. In cohesive powders, the aggregates are clumps of the powder mixture that, if not dispersed properly, can lead to varied and uneven mixing in the vessel.
In many cases, cohesive powder mixtures require milling or sieving to break up the aggregates. Additionally, larger powder particles may be dry-coated with a smaller particle to reduce interparticle forces and the tendency for aggregate formation.
Due to their mixing intensities and mechanisms, traditional powder blending methods such as shear, diffusive, and convective are only effective at blending certain types of powder mixes and are often very slow and ineffective and creating complete uniformity.
They are generally not capable of mixing both free-flowing and cohesive powder mixtures. Thus, historically, a mixing technology has been selected based on the specific powder properties for a given mixture including flow characteristics and particle size.
How to Mix Powders Evenly
ResonantAcoustic® Mixing (RAM) is a game-changer for powder mixing, as it mixes powders more evenly and faster than any other mixer. For those who have used it, RAM is the greatest powder mixing system ever made.
Powders of nearly any size, material characteristic, or morphology are usually thoroughly mixed using RAM technology in just 30 seconds – including both free-flowing and cohesive powders.
The Ultimate Industrial Powder Mixer - Resonant Acoustic Mixing (RAM)
When it comes to finding the right industrial powder mixer, RAM mixers are the clear choice. In fact, RAM mixes solids 10x to 100x times faster and more uniformly than any traditional mixing methods. RAM’s unique sound-energy motion causes each powder particle to randomly collide with adjacent particles. It causes them to divert their paths, collide and re-collide with other particles that are behaving in equally chaotic fashion to accomplish rapid and complete mixing. RAM’s powder and solids mixing capabilities include:
Similar or Dissimilar Particle Sizes. RAM can effectively mix both similar and dissimilar particle sizes and achieve a uniform final blend.
Particle Coating. Static and other physical forces combine to thoroughly coat particles, one material on another, layer upon layer.
Milling and Nano Coating. Coating larger particles with smaller ones is a common processing application, and milling is often a part of the same process.
This high speed video clearly illustrates the dispersion of carbon black particles, their de-agglomeration, and progressive and comprehensive coating of the plastic pellets in just 8 seconds!
Industry Expert Testimonial - NASA recently invented a new high temperature 3D-Printed GRX-810 superalloy with almost double the tensile strength, more than double the ductility, and orders of magnitude (10X-2000X) better creep rupture life than conventional superalloys and current 3D-printable metal parts.
GRX-810 cannot be produced by conventional machining, and is 3D-printed. GRX-810 can be used in space launch systems, aerospace and aeronautical applications, heat exchangers in nuclear power plants and other extreme temperature environments, thanks to RAM technology.
GRX-810 is made by coating NiCoCr metal powder with a film of nanoscale Y2O3 oxide particles using RAM technology.
Prior attempts to mechanically alloy the Y2O3 onto the metal powder with traditional equipment had deformed the powder. It became more platelet-like, had a tendency to stick, and as a result was much more difficult to print.
RAM rapidly and powerfully, yet gently coats the metal powder with the ceramic, without deforming the powder. The powder remains very spherical and flows well through the 3D printer.
The video short below tells the story in 60 seconds:
De-agglomeration. Agglomerated materials are separated into uniform particles that are separated rapidly with sieving attachments.
Milling, Size, & Morphology Changes. With the selection and addition of appropriate milling media, RAM can also be used to reduce particle size or change particle morphology of many materials.
Sieving. RAM technology can be used to separate mixed particles of varying sizes using common sieves. Low frequency operation speeds separation and flow-through to cleanly and thoroughly segregate particles without “bounce-back.”
RAM Mixers Make Powder Mixing Unbelievably Fast with Unmatched Uniformity
With Resodyn's cutting edge industrial powder mixers, you don't need to know special blending techniques or have a giant recipe book. Because of what we've already discussed, Resodyn mixer's mix powder 10x to 100x faster and much more uniformly than any other powder mixing machine on earth! So you can leave the techniques and tricks to the other guys because our mixing technology speaks for itself.
Resodyn's Acoustic Mixers are Perfect for Powders of All Types and Sizes
Resodyn's industrial mixing and processing products are proudly made in the USA and are in use in more than 40 countries around the globe.
Resodyn’s mixers feature universal processing technology for mixing virtually any kind of material without blades, propellers, paddles, or any other internal engineered mechanical devices.
RAM mixers deliver flexible, reliable, and repeatable performance in countless industrial applications from bench-scale development through continuous volume production.
Resodyn’s highly experienced team works with customers to mix virtually every combination of ingredients including liquids, pastes, and powders ranging from nano sizes to large particles as well as highly viscous materials.
Resodyn mixers and processors provide advanced solutions for a broad range of difficult industrial mixing and processing challenges across sectors such as pharmaceuticals, batteries, electronics, energetics, adhesives, cosmetics, and ceramics, as well as many other industries.