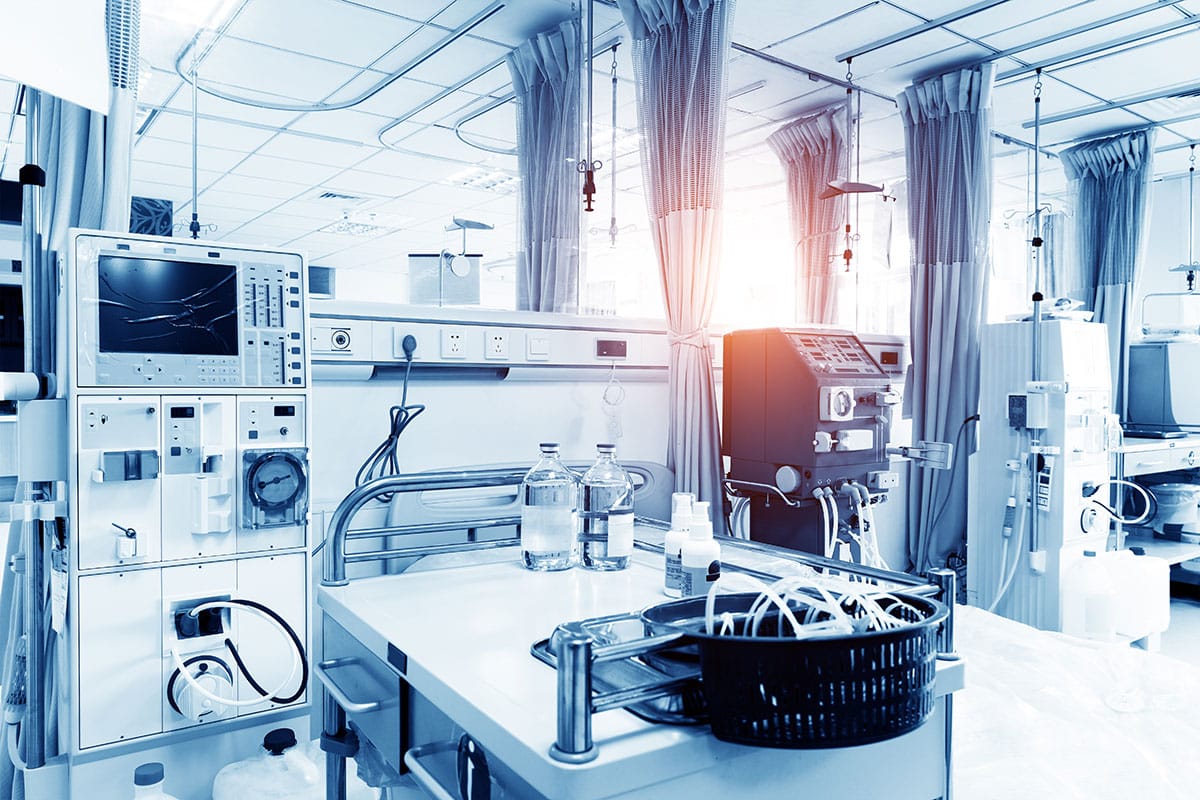
How RAM Mixers are Disrupting the Medical & Pharmaceutical Mixing Industries in Amazing Ways
Industrial mixing is often viewed as the combination and subsequent blending of raw ingredients. However, for most mixing industries, including the pharmaceutical and medical industries, this is a huge oversimplification.
Mixing often demands a great degree of accuracy and precision. When manufacturing pharmaceutical and medical products, the mixing step has an even higher level of complexity with sterility and sanitation requirements, and because the pharmaceutical blending process influences the ability of the product to work as intended.
Product stability and aesthetics of the final product are also directly tied to mix processes. Pharmaceutical and medical companies must perform the mixing step to support their customers, their brand, and their financial success.
Mixing Challenges for Pharmaceutical and Medical Industries
There are many challenges that impact mixing in pharmaceutical and medical operations, and the following highlights three of these obstacles: contamination, scalability, and materials processing.
-
Contamination
When people think about manufacturing pharmaceuticals or medical products, strict regulations and standards may come to mind. This is because these industries have stringent hygiene and cleanliness rules in place to ensure final products are safe for users.
Pharmaceutical and medical manufacturers typically have rigorous sanitary procedures in place for the equipment and processing area, and many processes require a sterile clean room with all surfaces sanitized. For these reasons, contamination mitigation presents a major challenge. Traditional mixers used in pharmaceutical applications often include special design features such as smooth vessel walls and mixing blades, and specialized materials to minimize risks of contamination when attempting to clean and avoid cross contamination.
2. Scalability
Most new pharmaceutical formulations are first trialed on a laboratory or small-scale basis. If successful, the formulation is then scaled up to larger production runs. Scalability presents a major challenge for most industries but is especially difficult for pharmaceutical and medical product companies to achieve.
3. Uniformity
For these sectors, the proper functioning of active and non-active ingredients in a formulation is critical to the effectiveness and medical benefit of the final product. If the mix results change even slightly, the final product may be less effective for (or even harmful to) the patient. Precise reproduction of the intended ingredient mix results, as well as material properties such as cohesiveness, viscosity and density, presents a major challenge when scaling pharmaceutical and medical mixing from laboratory to pilot and volume production.
4. Materials Processing
As with other industrial mixing sectors, pharmaceutical and medical mixing presents difficulties with materials processing for all types of raw ingredients. These include powders, liquids, and slurries. For example, dissimilar fluids can be very complicated for traditional mixing methods to effectively and uniformly blend within an acceptable timeframe.
Powder mixes also offer challenges as well as it is difficult to ensure uniform mixing and avoid segregation of the ingredients while retaining effectiveness. As the viscosity of raw ingredients increases, mixing requires additional energy to blend with traditional motor-driven units, which in turn drives up operational costs and increases production cycle times. The issue of materials processing is amplified for pharmaceutical and medical processes due to the precision and uniformity required during the mixing step.
How RAM Mixers are Disrupting the Pharmaceutical Blending Industries in Powerful Ways
ResonantAcoustic® Mixing (RAM) technology solves the mixing challenges previously discussed as well as other problems encountered by the pharmaceutical mixing and medical blending industries.
RAM addresses the challenge of contamination with its single technology platform. The world’s top pharmaceutical firms already rely on RAM’s ability to instantly switch from one set of ingredient characteristics to another, while changing only the processing vessel and the mixing parameters. Cross-contamination, excess movement, and material handling are eliminated almost instantly.
RAM Can Mix Virtually Anything at Any Scale
Regarding materials processing, RAM can efficiently mix virtually any combination of materials. Its intense yet gentle technology processes materials of nearly any particle size or behavior. Whether cohesive, agglomerated, nano-scale, or temperature-sensitive, a RAM mixer can control temperatures, apply vacuum, dry or spray-coat one particle on another, and effectively process any combination of powders, liquids, highly viscous or solids-loaded materials.
Click here to watch a video that demonstrates RAM’s ability to uniformly blend dissimilar powders in just 10 seconds!
Exceptional Uniformity for Pharmaceutical Blending
RAM is known for its precise and uniform blending on all levels: macroscopic, microscopic, and even molecular. This method is inherently reproducible, resulting in high quality and consistent products while reducing waste and costs associated with poor, off-spec batches. This level of accuracy is critical for pharmaceutical and medical mixing.
10x to 100x Faster Mixing/Processing Times
RAM also solves the problem of productivity by reducing processing time - often dramatically - while increasing quality and consistency of batches. RAM technology uses low-frequency sound energy to thoroughly mix particles of often vastly different characteristics. Mix times of hours are frequently reduced to minutes, and previously unmixable ingredients are dispersed uniformly and thoroughly – all but eliminating mixing as a bottleneck in the manufacturing process.
Resodyn Manufactures World Class Pharmaceutical Mixers
From the world's top pharmaceutical companies to international manufacturers, global tech giants, and nearly every U.S. National Laboratory, Resodyn Acoustic Mixer installations in over 40 countries are in use today around the globe, and all share a single, powerful technology platform. Whether developing new materials in the laboratory or running full-scale industrial production, RAM systems are available in configurations to fit your application.
Resodyn is the only company in the world to offer RAM technology, and provides pharmaceutical mixers geared towards the specific needs of pharmaceutical and medical industries. Here are some additional details highlighting Resodyn's pharmaceutical mixers:
PharmaRAM I
This mixer has a 500-gram capacity for small sample processing. PharmaRAM I is easy to operate with simple controls that allow rapid processing of small samples. It is built on the same technology platform and operating system as Resodyn’s PharmaRAM II for repetitive and precursor processes, and includes vacuum temperature monitoring capability.
PharmaRAM II
This unit has a 1 kg capacity and offers bench-scale development capabilities. PharmaRAM II includes an onboard operating system with recipe development and memory, real-time parameter monitoring, 100% processing data retention, and multiple operator security levels, as well as temperature control capability. RAM technology scales easily without additional testing from development to pilot to production scales.
OmniRAM Pharma
OmniRAM Pharma has 11 lb (5 kg) payload capacity, and is a full-featured, digitally controlled batch mixer for larger than bench scale development, clinical trials, pre and small-scale production and processing.
RAM 5 Pharma
This mixer has 80 lb (36 kg) capacity for pilot and production scale. It allows fast and efficient scaling from pre-production bench-level scale. RAM 5 Pharma is available with a full menu of processing options, including temperature monitoring and control, mixing under vacuum. Standard functions include recipe development and retention, real-time parameter monitoring and recording, 100 percent processing data retention, multiple operator security levels, and multiple mixing vessel options.
RAM 55 Pharma
With the batch payload capacity of up to 924 lbs (420 kg) PharmaRAM 55’s digitally controlled, multiple processing capabilities multiply RAM’s value through direct and easy scale up from the bench development to larger scale batch production.
Change the way you think about mixing and processing with a RAM demonstration either by remote/online presentation or on-site at your facility, using your own materials, and solving your unique mixing challenges.
Contact Resodyn today to learn more about how RAM can benefit your pharmaceutical or medical mixing process and to schedule a free demonstration.