Home » Applications » Powders and Solids
HOW RAM MIXES POWDERS & SOLIDS 10x TO
100x FASTER WITH UNBEATABLE UNIFORMITY
Powders of nearly any size, material characteristic, or morphology are rapidly and thoroughly mixed using RAM technology.
Additionally, RAM processing is frequently 10x to 100x faster than traditional technologies!
The RAM platforms's rapid, 60Hz motion causes each particle to randomly collide with adjacent particles, diverting their paths, colliding and re-colliding with other particles behaving in equally chaotic fashion.
Similar or Dissimilar Particle Sizes
Chaotic particle collision and large scale vapor migration speed dispersion and ultra-high uniformity.
Particle Coating
Static and other physical forces combine to thoroughly coat particles, one material on another, layer upon layer.
Deagglomeration
Agglomerated materials are separated into uniform particles that are segregated rapidly with sieving attachments.
Milling, Size, & Morphology Changes
With the selection and addition of appropriate milling media, RAM can also be used to reduce particle size or change particle morphology.
Sieving
RAM technology can be used to separate mixed particles of varying sizes using common sieves. Low frequency operation speeds separation and flow-through of particles to cleanly and thoroughly segregate particles.
HOW RAM POWDER MIXERS
GIVE YOU INCREDIBLE RESULTS
The Mechanics of RAM Powder Mixing
RAM technology drives particle to particle collision and generates large-scale vapor migration, vastly improving both modes of powder mixing.
ResonantAcoustic® Mixing:
- Vertical vessel movement 60 times per second at up to 100 g of acceleration generates intense particle motion
- The primary mixing mechanism is particle redistribution driven by inter-particle collisions
- Particle motion is entirely random, preventing de-mixing
- Active vapor pockets move rapidly throughout the powder matrix creating highly active mixing zones
How RAM Compares to Other Mixing Methods
At small scale, diffusion blending
At scale, bulk mixing blending
Traditional tumbling methods use a single g of gravity to circulate mixing powders in small scale particle cascading
Using less than 30 rpm, traditional methods must avoid centripetal motion to keep particles involved in mixing
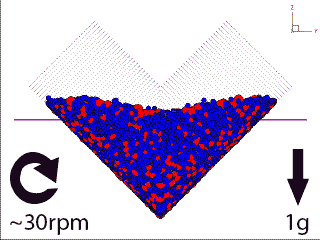
RAM generates up to 100 g of acceleration driving chaotic motion through the mixing media
RAM uses intense chaotic motion without any centripetal forces or de-mixing phenomena
WATCH TO LEARN ABOUT POWDERS
AND SOLIDS MIXING WITH RAM
Dissimilar Powder Mixing In 10 Seconds!
Dry ingredients can be difficult to thoroughly and consistently mix, particularly when the particles are of different sizes and characteristics. To illustrate effective and rapid mixing, 10 grams of fumed silica is blended with 100 grams of sand in only 10 seconds. Completed specimens exhibit no airborne fumed silica, demonstrating uniform blending at an order of magnitude difference in particle size.
Experience the Unmatched Speed and Precision of ResonantAcoustic® Mixing (RAM)
ResonantAcoustic® Mixing has transformed the pharmaceutical and biotechnology mixing landscape, setting a new standard of excellence. RAM enables the mixing of powders, liquids, slurries, or pastes at almost any scale, all without the risk of cross-contamination.
Milling and Nano Coating in 8 Seconds!
Coating larger particles with smaller ones is a common processing application, and milling is often a part of the same process. In this video, agglomerated carbon black particles are simultaneously milled to nano size particles that coat the plastic pellets completely in just a few seconds. The high speed video clearly illustrates the dispersion of carbon black particles, their de-agglomeration, and progressive and comprehensive coating of the plastic pellets.
NASA Invents GRX-810 SuperAlloy with RAM
NASA recently invented a new high temperature 3D-Printed GRX-810 superalloy with almost double the tensile strength, more than double the ductility, and orders of magnitude (10X-2000X) better creep rupture life than conventional superalloys and current 3D-printable metal parts.
GRX-810 cannot be produced by conventional machining, and is 3D-printed. GRX-810 can be used in space launch systems, heat exchangers in nuclear power plants and other extreme temperature environments, thanks to RAM technology.
GRX-810 is made by coating NiCoCr metal powder with a film of nanoscale Y2O3 oxide particles using RAM technology.
Prior attempts to mechanically alloy the Y2O3 onto the metal powder with traditional equipment had deformed the powder. It became more platelet-like, had a tendency to stick, and as a result was much more difficult to print.
RAM rapidly and powerfully, yet gently coats the metal powder with the ceramic, without deforming the powder. The powder remains very spherical and flows well through the 3D printer.
NEED HELP WITH
A CHALLENGING MIX?
We love challenges! Get in touch with us for a FREE mix test or an onsite or virtual demo.
Testimonials
"RAM is promising route for primer formulation processing. It minimizes safety concerns with mixing, and exhibits great potential for dry mixing…”
“…[We had] challenges with mixing transdermal pharmaceutical products, particularly with mixing a viscous (~10,000cp) solids-loaded cream consisting of water, excipient, API, and a sticky acrylate adhesive. It used to take multiple material addition steps and up to eight hours with an overhead stirrer to achieve desired uniformity. With a LabRAM we performed the mix in a little more than two minutes…”
Corium, a U.S. biopharmaceutical company