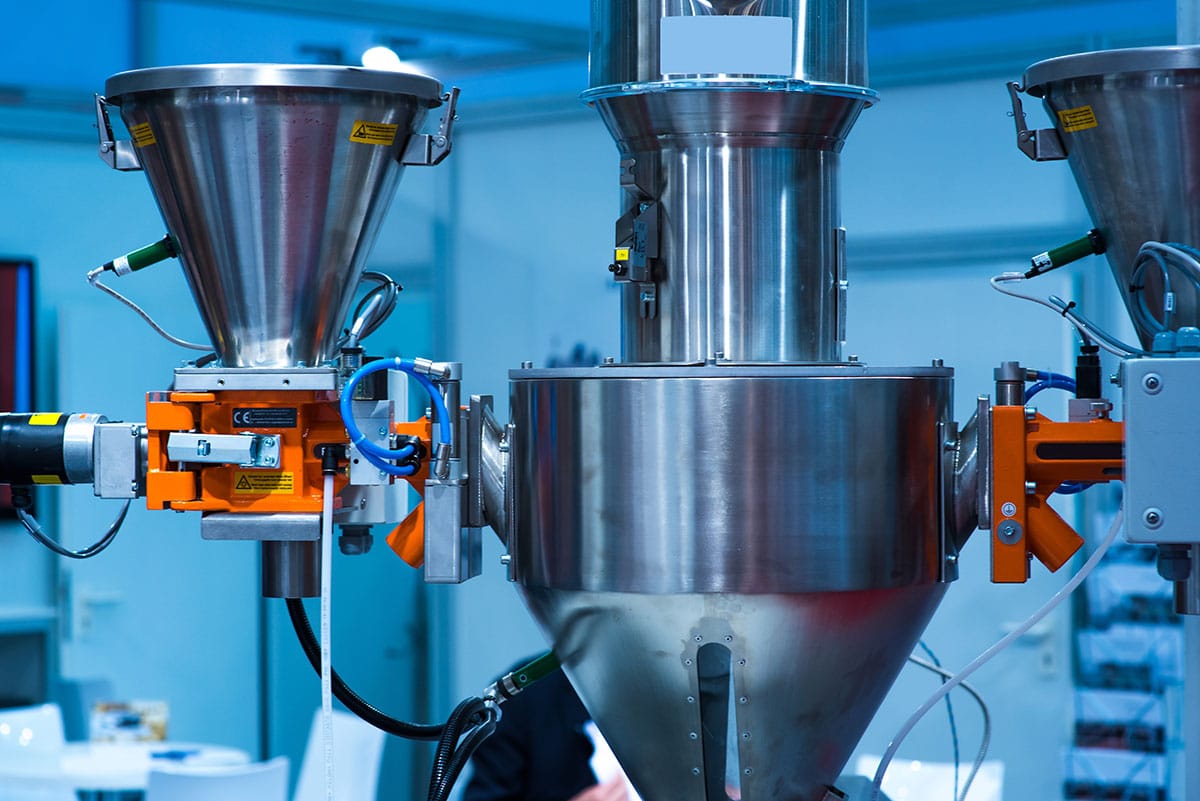
How to Overcome Mechanical Restrictions in Material Mixers
Mechanical material mixers are common industrial mixing devices found in nearly every industry. These systems are generally comprised of three parts:
- an impeller,
- a shaft, and
- a drive mechanism.
Mechanical material mixers employ a drive mechanism, often an electric, hydraulic, or pneumatic motor. The motor rotates a shaft with one or more attached blades or impellers to agitate the ingredients within a mixing vessel to create mixing zones at their edges. The shaft can be oriented vertically, horizontally, or at an angle.
Impeller types include propellers, paddles, blades, and other engineered devices. The type and size of impeller used can be limited and therefore specialized by factors such as the viscosity of the materials and the level of shear that may be required. In general, impellers drive either radial or axial flow within a vessel.
Axial impellers generate more vertical movement within the vessel and typically cause the contents to move between the top and bottom. Radial impellers drive horizontal movement, pushing vessel contents in the direction of the walls of the vessel.
How RAM Overcomes Mechanical Restrictions in Mixing Materials
These internal elements of a mechanical material mixer present several challenges. Below are some of the difficulties associated with mechanical mixers and an explanation of how Resodyn’s ResonantAcoustic® Mixing (RAM) technology overcomes or avoids each of these challenges.
RAM technology uses acoustic, or sound energy to generate uniform, pervasive material movement and sound-induced (acoustic) interactions that swiftly result in optimal and uniform mixing.
In addition to acoustic energy, RAM mixers generate and control rapid and relatively large-scale vertical motion to drive movement of the mixer’s resonator plate and thus the contents of the mixing vessel itself. Conditions within a RAM vessel are continuously monitored and adjusted to achieve and maintain a “resonant state.” The resonant state is proven to generate the highest rate of energy transfer to optimize mixing while consuming the least amount of power to maintain that level. This results in a very fast, efficient, and effective mixing results.
Quality and Uniformity
A key to effective mixing is the creation of turbulent conditions within the vessel. Impellers create turbulence, but only in the region closest to the impeller, which creates “dead spots” of unmixed material in the vessel. This issue exists for all types of ingredients but is especially true for viscous materials. To improve mixing efficiency, mechanical mixers are often outfitted with multiple impellers, and in some cases baffles. Even with these additions, long mixing times (compared to RAM) are needed to approach the desired uniformity and homogeneity in the final blend. Even so, mechanical approaches often fail to achieve this regardless of the length of processing time.
RAM employs low-frequency energy to generate unique material movement and sound-induced material interaction within a vessel. The combined energy imparts up to 100 times the force of gravity or 100 g into the mixing ingredients. This causes the ingredient particles of a dry or powder mix to continuously collide in a random, chaotic pattern throughout the entire vessel, which results in immediate and continuously efficient mixing. RAM achieves precise and uniform blending with all particulate size levels: macroscopic, microscopic, and even molecular. The results of this method are consistently reproducible, resulting in high-quality, uniform products without the waste and costs associated with failed, off-spec batches. RAM mixers are extremely efficient and dramatically reduce mix times versus traditional mixers (in many cases from hours to minutes).
Shear Forces
Mechanical mixing relies on the power of a motor-driven impeller to generate movement and mixing within a mixing vessel. The force of the impeller or other engineered device generally referred to as “shear,” often results in particle breakage and morphology changes, as well as significant stress on the mixing technology used. When fluids are mixed, especially viscous materials, stress and friction are created among the particles as they move. These are called shear forces and often result in unintended or unwanted damage to individual particles. Particle structures may be torn and the overall particle size in the vessel may decrease. In general, the more rapidly the blade moves through the vessel, the more shearing is likely. Many manufacturers extend the mixing cycle or reduce rpm of the axle to avoid high shear stresses and preserve particle integrity, which in turn results in longer mix cycle times.
RAM technology is a “non-contact” mixing method. It does not require use of impellers, blades, paddles or other engineered devices to facilitate mixing. Since there are no internal, mechanically-driven devices that can damage or destroy particles, RAM mixers preserve material integrity and consistently repeatable results in the final product, regardless of material viscosity.
Energy Consumption
Mechanical material mixers often overheat or grind to a halt when processing high viscosity materials beyond the mixer’s capacity. Larger-horsepower motors may be used in these cases, but energy efficiency declines significantly, which in turn drives up operating costs. Additionally, the large amount of energy created by the impeller does not dissipate well in viscous materials and can result in excessive heat build-up. To manage this issue, some mechanical mixing products require additional cooling or heat exchange and temperature control equipment.
Every highly-viscous mixing process involves wetting, incorporation, and mixing phases. Without the mechanical limitations of traditional methods that require all materials to pass through a mixing zone close to the impeller, RAM technology performs all three steps simultaneously and consistently throughout the mixing vessel, reducing processing time by orders of magnitude. Since RAM does not have an internal impeller, it does not have the energy-consuming drawbacks that traditional mechanical mixers have and is, thus, able to mix high viscosity materials effectively without the risk of overheating or mechanical failures.
The Hidden Cost of Clean-up
The comparison above highlights one of the primary differences between RAM and traditional mixing technologies. Processing impurities and contamination are less and less tolerable in nearly every industry. This requires extensive and meticulous cleaning practices, procedures, and materials for every device touching the processed product. Labor, vessels, blades and impellers, cleaning fluids and other cleaning accessories add zero value cost to every batch of traditionally processed material. Other than re-usable vessels, RAM eliminates the necessity, cost, and time to achieve hygiene and cleanliness.
About Resodyn Acoustic Mixers
Resodyn industrial mixing and processing products are made in the USA with installations in more than 40 countries today. Resodyn’s mixers feature universal processing technology for mixing virtually any kind of material without blades, propellers, baffles, or any other internal engineered mechanical devices. RAM mixers deliver flexible, reliable, and repeatable performance in countless industrial applications from bench-scale development through continuous volume production.
Resodyn’s highly experienced team works with customers to mix virtually any combination of ingredients including liquids, pastes, and powders ranging in sizes as small as nano particles as well as highly-viscous materials. Resodyn products provide advanced solutions for a broad range of difficult industrial mixing and processing challenges across sectors such as pharmaceuticals, electronics, energetics, adhesives, cosmetics, ceramics, and many other industries.
Resodyn is the only company in the world to offer RAM technology and its unique benefits. It is a ground-up departure from traditional industrial mixing methods, and there’s no better way to understand the difference than seeing RAM in action. Request a RAM demonstration today, which can be performed live on-line or on-site at your facility, using your own materials, and solving your uniquely specific mixing challenges. Contact us today to learn more about how RAM can improve your mixing process and schedule a free demonstration!