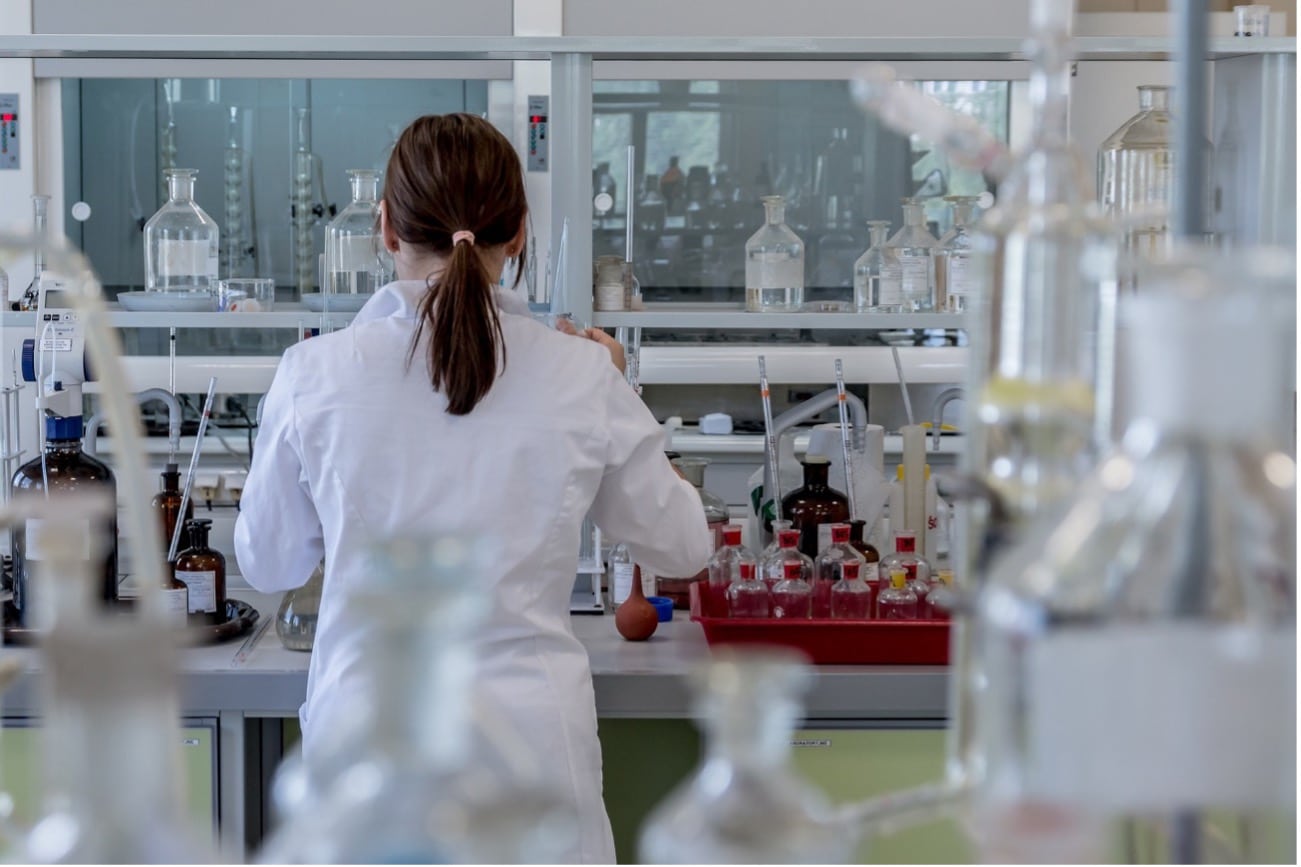
RAM Mixing Systems Seamlessly Scale for Pharmaceutical Blending
Selecting the right pharmaceutical blender design for the final product used to be a difficult decision because of the various ingredients and mixers needed.
In pharmaceutical blending, various ingredients are used depending on the formulation and intended use. Common ingredients include:
- Active Pharmaceutical Ingredients (APIs): The primary ingredients that provide therapeutic effects.
- Excipients: Inactive substances that serve as carriers for the API. They can include:
- Fillers: Such as lactose, microcrystalline cellulose, or starch, which add bulk.
- Binders: Like polyvinylpyrrolidone (PVP) or hydroxypropyl methylcellulose (HPMC), which help hold the mixture together.
- Disintegrants: Such as croscarmellose sodium or sodium starch glycolate, which promote the breakdown of the tablet.
- Lubricants: Such as magnesium stearate or stearic acid, which prevent ingredients from sticking to equipment.
- Glidants: Such as talc or colloidal silicon dioxide, which improve powder flow properties.
- Coatings: For tablets, these may include film-forming agents like HPMC or enteric coatings that prevent dissolution in the stomach.
- Preservatives: To prevent microbial growth in liquid formulations, common preservatives include parabens or benzalkonium chloride.
- Stabilizers: To enhance the stability of the formulation, such as ascorbic acid or citric acid.
The specific choice of ingredients depends on the desired properties of the final product, such as bioavailability, stability, and release characteristics.
PharmaRAM Mixers Do It All in the World of Pharmaceutical Blending
But it is now easy-and there is no issue with scale of pharmaceutical product blending. Bench, pilot, or production volumes all mix the same when using the ResonantAcoustic® Mixing system from Resodyn Acoustic Mixers.
ResonantAcoustic® Mixing works with quality and speed:
- Seamless scaling from bench to pilot to production through continuous blending
- Non-contact blending – no blades are used
- Multiple combinations of powder types and semisolids
- Deagglomerates API aggregates without changing crystal habit
- Thorough homogenization for every blend
- Achieves RSD values as low as <1%
- One blender for all powder blending challenges
- Perfect blend -no over blending or un-mixing
- No cross-contamination
- 10x to 100x times faster than conventional blenders -reduce blending times from hours to minutes or even seconds
The best companies have moved away from legacy blender designs like ribbon, paddle, conical screw, or tumble. Instead they invest in tomorrow’s technology that's here today.