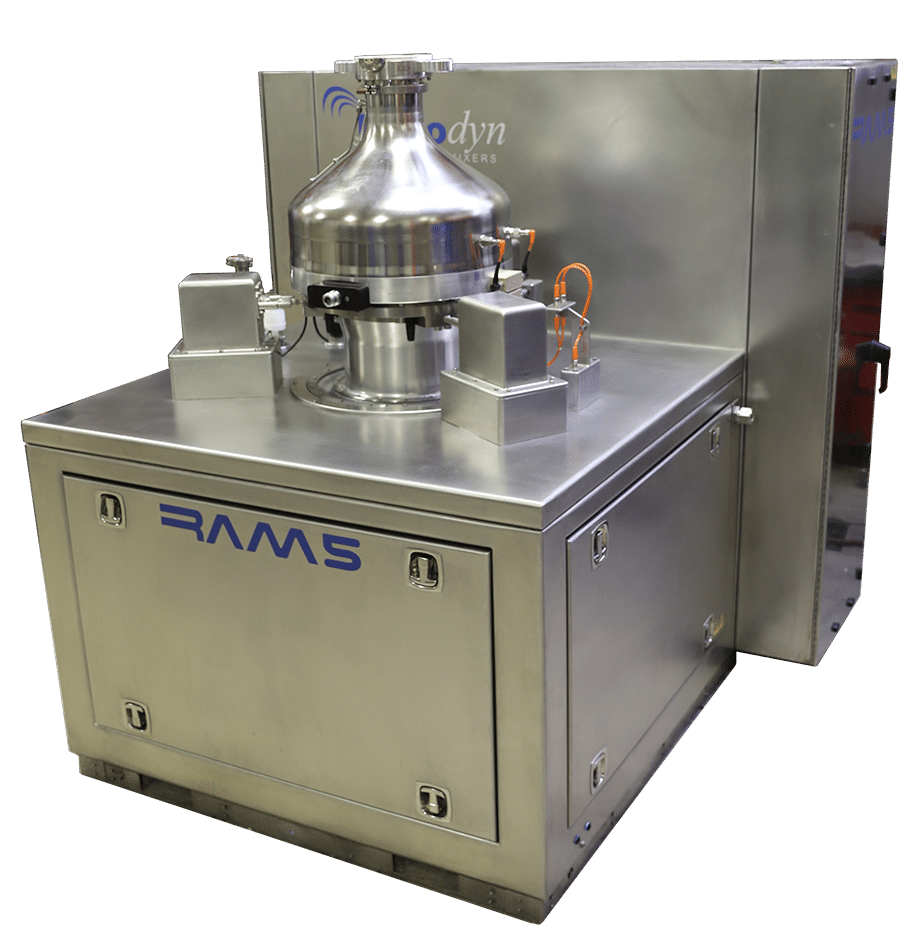
New Solutions for Industrial Mixing Challenges
Mixing is a key processing step in nearly every industry, from pharmaceuticals to lubricants to ceramics. Traditionally, mixing has been accomplished using motor-driven impellers, blades and other engineered devices that rotate in or otherwise agitate the ingredients. These methods, however, present several challenges including degradation of particles during mixing, non-uniform and inconsistent mix quality, and extended mixing times.
Fortunately, a new and innovative technology, ResonantAcoustic® Mixing (RAM), solves many of the problems that plague traditional mixers. RAM combines the efficient power generation of resonance and the effects of sound energy to facilitate mixing – without the use of impellers or other mechanical means within a mixing vessel.
Benefits of RAM Technology
RAM mixing and processing offers several advantages over traditional mixing techniques and delivers value to customers in a number of compelling ways. RAM technology’s benefits include:
- Outstanding mix quality: ResonantAcoustic® Mixing is known for precise and uniform blending on all levels: macroscopic, microscopic, and even molecular. This method is highly reproducible, and results in consistent high quality products while reducing waste and cost associated with off-spec mix batches. Additionally, when required for certain ingredients, RAM systems can incorporate specialized processing conditions that include mixing under vacuum, or at a controlled temperature mixing conditions that reduce the potential for failed batches and waste generation.
- Unrivaled speed: RAM mixers dramatically cut mix times vs. traditional mixers – in many cases from hours to just a few minutes. While highly effective at reducing mix times; RAM’s productivity improvements often extend beyond the mixing step and into downstream operations. The speed of RAM mixing also eliminates time-consuming, downstream “dead-spots” that reduce productivity delays due to traditional mixing technologies.
- Extreme versatility: ResonantAcoustic® Mixing can effectively blend virtually any combination of powders, liquids, highly viscous or solids-loaded materials. This technique offers significant flexibility in the size and design of the vessel used for mixing at the smaller, developmental scale, and makes precision mixing possible for a wide range of applications.
- Excellent scalability: Mixing technologies are often handicapped by their inability to scale effectively. RAM mixers, on the other hand facilitate scalability. RAM technology enables users to start by optimizing a given formulation on a small scale – less than 1,000 grams. The formulation can then be directly and seamlessly scaled to manufacturing volumes of 5 kg, 36 kg, 420 kg, as well as continuous operations with minimal variance of mix quality. No significant retesting or reformulating is routinely not required for most materials. The ability of RAM mixers to easily and directly scale recipes saves significant time and money – and get to market faster. Given RAM’s inherently minimal change-over and clean-up costs, these benefits lead to substantial cost savings and greater productivity and profitability for virtually any process.
So How Does Resonant®Acoustic Mixing Actually Work?
ResonantAcoustic® Mixing uses low-frequency energy to generate unique material movement and sound-induced (acoustic) interaction that rapidly results in optimal, uniform mixing. More specifically, RAM mixers generate and control vertical motion to achieve vibration and movement of its resonator plate, which transfers to the contents of the mixing vessel in use.
Instead of using impellers or other traditional mechanical mixing implements, RAM’s unique mixing technology combines low-frequency, high-intensity motion with the acoustic energy this motion creates. This acoustic energy is generated by the vertical motion of RAM’s resonator plate or mixing platform and attached vessel holder. At 60 times per second, RAM technology creates both motion of the ingredients inside the vessel as well as acoustic (sound) energy that emanates through RAM’s base during its upward motion, and repeated by the inside of the vessel’s lid during the downward motion, both of which act as a transducers. This sound energy generates a unique phenomenon that varies with the material being processed. The combined energy generated by the motion and sound energy is imparted to the vessel contents to cause rapid fluidization and dispersion, which in turn results in swift and effective mixing.
The operating conditions of the RAM system are continuously monitored and adjusted to maintain the “resonant state” of the mechanical system. The resonant state is proven to consume minimal power while achieving optimal mixing of ingredients, which in turn results in both a very efficient and effective process.
One of the reasons RAM systems are so effective is the system’s balance between frequency and displacement. Some mixing technologies, such as ultrasonics, operate at very high frequencies but achieve displacement only within a minute area directly around the frequency generating probe Other methods, such as those used in paint mixers, achieve a high displacement but operate at very low frequencies that can’t produce the mixing intensity and uniformity that is achieved by RAM mixing. The resonant state for RAM systems is typically at a frequency range of around 60 Hz with a relatively large displacement around 0.55 inches. This combination imparts a high level of energy, up to 100 times the force of gravity (or g) into the mixing ingredients, causing the particles to continuously collide in a random, chaotic pattern in the case of solids or powders. This results in immediate and continuously efficient and uniform mixing.
When mixing liquid ingredients, RAM technology creates a phenomenon known as Faraday instabilities within the ingredients. The surfaces of ingredient liquids become unstable, causing “fingers” and “cavities” to form at the liquid surface boundary or interface. This swiftly increases the surface area of the liquids and facilitates rapid and homogenous mixing of the ingredients. Click here to watch a video demonstrating the Faraday instabilities created within RAM mixers.
Resodyn’s Capabilities and Expertise
Resodyn industrial mixing and processing products are made in the USA and are in use in more than 30 countries today. Resodyn’s mixers feature universal processing technology for mixing virtually any kind of material without blades, propellers, baffles, or any other internal engineered mechanical devices. RAM mixers deliver flexible, reliable, and repeatable performance in countless industrial applications from bench-scale development through continuous volume production.
Resodyn’s highly experienced team works with customers to mix virtually every combination of ingredients including liquids, pastes, and powders ranging from nano sizes to large particles as well as highly viscous materials. Resodyn products provide advanced solutions for a broad range of difficult industrial mixing and processing challenges across sectors such as pharmaceuticals, electronics, energetics, adhesives, cosmetics, and ceramics, as well as many other industries.
Resodyn is the only company in the world to offer RAM technology and its unique benefits. It is a ground-up departure from traditional industrial mixing methods, and there’s no better way to understand the difference than seeing RAM in action. Request a RAM demonstration today, which can be performed live on-line or on-site at your facility, using your own materials, and solving your uniquely specific mixing challenges. Contact us today to learn more about how RAM can improve your mixing process and schedule a free demonstration!