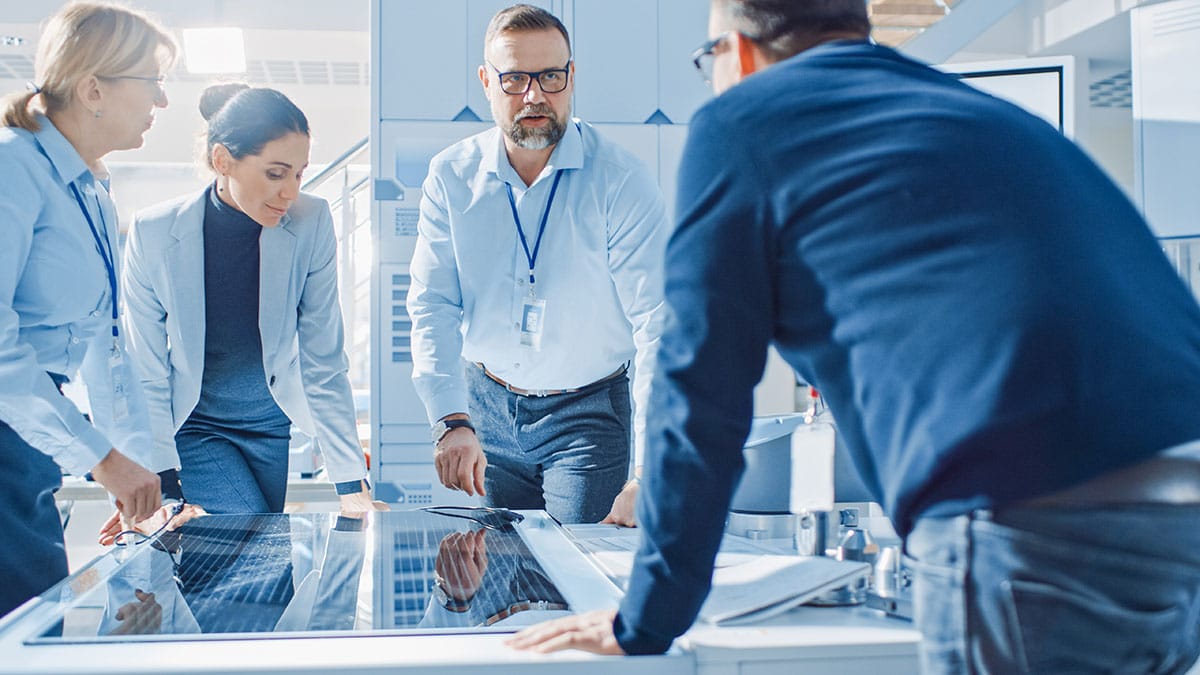
Four Current Trends in the World of Industrial Mixing Technology
From food and beverage production to fertilizer plants to pharmaceutical operations, mixing is a key step in nearly every manufacturing process that involves material processing. As blends and products become more customized and complex, industrial mixing technologies must be capable of addressing an increasing number of challenges. Manufacturers demand mixers that are not only efficient and cost-effective, but provide flexibility and the ability to scale production to meet their needs. Significant advancements in mixing have been made in recent years, and these are some of the current trends in industrial mixing technology:
1. Energy Efficiency. Manufacturers will capitalize on any opportunity to reduce operating costs without sacrificing quality. Reduction of energy consumption is one means of doing so. Consistent with the trend in recent years toward more environmentally-friendly and sustainable manufacturing, new models of mixing equipment are typically more energy efficient than previous generations. In many instances, advancements in mixing technologies make it feasible to achieve desired mixing results using less energy. There is still a large gap that exists with energy usage across mixing technologies, however. For example, traditional mechanical mixers are inherently inefficient because they require lengthy mixing times to achieve desired mix results. Longer mix times mean higher, costly energy consumption, but without improvement to quality or repeatability. Furthermore, as viscosity of raw ingredients in mixes increase, traditional mixers require additional energy to blend with their motor-driven units, further increasing operational costs and cycle times. Resodyn’s ResonantAcoustic® Mixing (RAM) technology, on the other hand, is extremely efficient relative to mechanical mixers. It dramatically reduces mix times versus traditional mixers (in many cases from hours to minutes). ResonantAcoustic® technology harnesses the power of the resonant condition. This has two main effects, the ability to generate high power levels in relatively small packages, and by the nature of resonance, require very little energy to maintain the resonant condition. RAM operations minimize environmental impact with lower, overall energy consumption and faster cycle times, even when mixing viscous materials.
2. Higher Volume Operations. Companies that need industrial mixing solutions increasingly demand mixing equipment capable of higher production throughput. One way companies achieve ever-greater production volumes is through the adoption of continuous operations. The additional capacity gained from continuous processing enables more flexibility to scale operations as needed. Resodyn’s Continuous Acoustic Mixer (CAM) system is an excellent option for companies that would benefit from continuous mixing. This technology enables RAM mixing to address high throughput needs. Additionally, each CAM system delivers an environmentally-friendly Clean in Place (CIP) process that enables no-contact, no-disassembly cleaning, which dramatically reduces waste and minimizes risks of contamination.
3. Improved Process Hygiene. Improving the cleanliness of mixing operations leads to better manufacturing efficiency due to a reduction of contaminants and off-spec products. It also results in less downtime for cleanup and changeover procedures. Hygienically-clean equipment is crucial when processing perishables, pharmaceuticals, or other products that require exacting purity. Even a trace of impurities can have significant consequences, so these processes require more thorough and frequent sanitation to prevent contamination. Traditional mixer configurations involve mechanically-driven internal parts that are difficult and time consuming to clean and prone to introducing impurities. To improve cleanliness of traditional mixers, one approach involves the use customized mixing fittings and connectors to avoid leaks due to a poor fit. Some companies are using spare components to swap out parts during cleaning to reduce the production slowing downtime required to clean a given part. Another trend in mixing technology is the use of clean-in-place equipment, where cleaning steps are automated and customized to suit the specific mixing application. Alternatively, the RAM method of mixing does not utilize internal, engineered components that need cleaning and otherwise complicate sanitation steps, which allows for easier and faster cleanup, changeover, and maintenance.
4. Increased Customization. There is a trend towards more varied and customized formulations and products across many industries, including pharmaceuticals and food production. This sometimes leaves manufacturers scrambling to find mixing equipment and accessories that will effectively mix a newly revised set of ingredients and achieve the desired outcome of the mixing step. Unfortunately, the plethora of mixers and accessories available on the market, with combinations focused on mixing specific sets of ingredients, makes most mixing systems inflexible and unable to easily switch formulations without sacrificing efficiency or uniformity. RAM does not require such customization, because its acoustic mixing technique provides ample operations flexibility. This is due to its proven approach to instantly and continuously achieving effective material movement throughout the entire mixer vessel. RAM achieves precise and uniform blending on all particulate size levels: macroscopic, and microscopic,. The results are consistent and highly reproducible, which results in high quality, faster inspection, and uniform products.
About Resodyn
From the world's top materials processing companies to international manufacturers, global tech giants, and nearly every U.S. National Laboratory, organizations in more than 40 countries rely on Resodyn ResonantAcoustic® Mixers’ single, powerful technology platform. Whether used for development of new materials in a laboratory or for running full-scale industrial production, RAM systems are available in configurations to fit applications across dozens of industries.
Resodyn is the only company in the world to offer RAM technology. Change the way you think about mixing and processing with a RAM demonstration: on-line or on-site at your facility, using your own materials, and solving your mixing challenges.
Need help with a challenging mix? There is no better way to understand the RAM difference than seeing the technology in action. RAM sales professionals deliver high value, on-site application presentations, product technology demonstrations, and even mixing tests using your own materials, without cost to you.
Contact us today to discuss your requirements or to schedule a free demo.