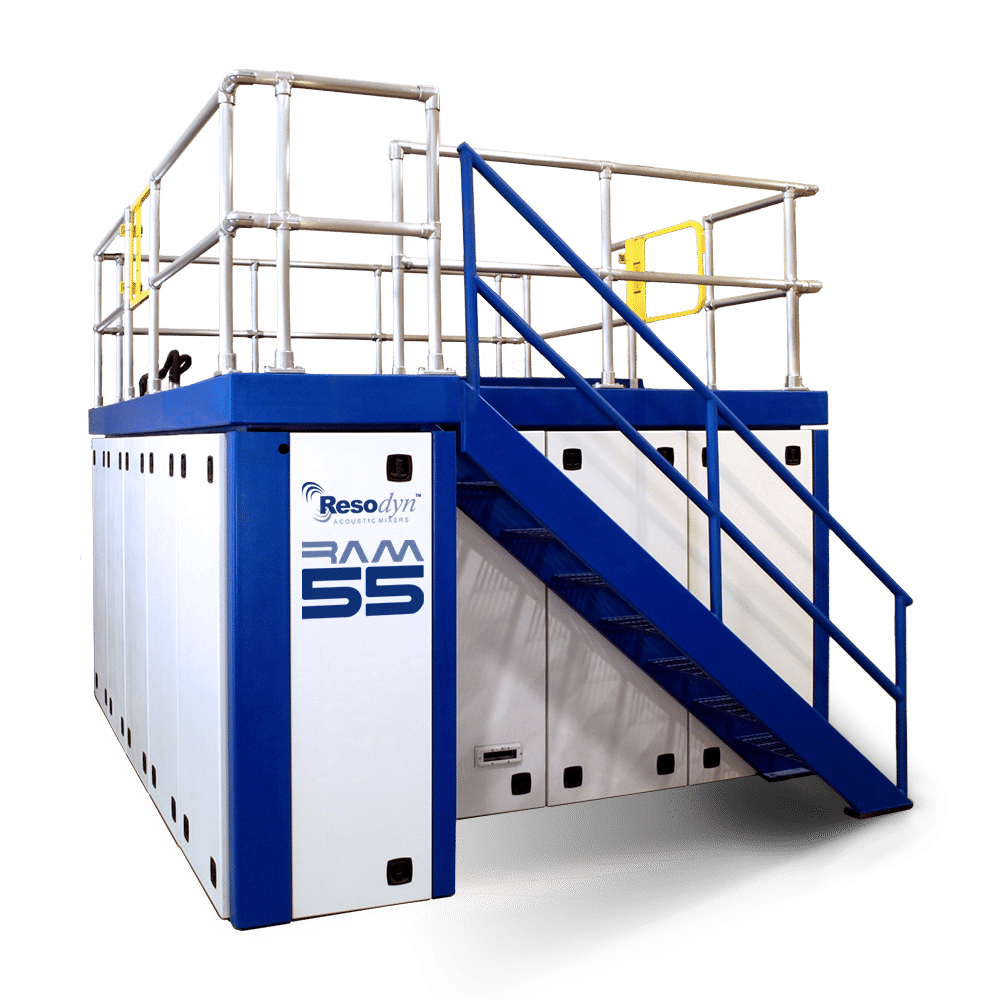
In today’s competitive environment, OEMs in every industry are looking for opportunities to reduce costs while maintaining or increasing quality. Industrial mixing steps are often labor and time-intensive, and poor mixing can lead to low yields, contamination, errors, and excessive . Each of these ultimately result in higher labor costs due to rework necessary to correct the low-yield problem. For these reasons, the materials mixing step can be a great opportunity for operational improvements that reduce costs and improve efficiency. Consider these three ways organizations can reduce labor cost in mixing operations: reduction in mixing times, elimination of steps that add no value, and consideration of continuous operations.
1. Reduce mixing cycle times
The old adage “time is money” applies to most things in business, including industrial mixing operations. The simplest way to decrease labor cost is to reduce cycle times, but this is easier said than done when working with traditional mixing methods. Traditional mechanical mixers are inherently inefficient and often require lengthy mixing times to achieve desired mix uniformity. Such inefficiencies result in higher energy consumption, longer mix cycle times, and higher labor costs without the benefits of improvement in quality or predictable, repeatable results.
In an effort to reduce cycle time, OEMs often add internal accessories such as baffles and multiple agitators to overcome highly limited number of mixing areas in traditional configurations. These add-ons are limited in what they can do, and often do not yield desired performance. Many OEMs turn to ResonantAcoustic® Mixing (RAM) to reduce mixing cycle times. RAM technology combines the power of resonance and sound energy mix ingredients in every part of the vessel, instantly, and continuously. RAM creates more efficient mixing without the use of impellers or other engineered devices within a mixing vessel. RAM mixers’ efficiency dramatically reduces mix times compared to traditional mixers. In many cases RAM reduces mix times from hours to minutes. Additionally, RAM’s productivity improvements and benefits often extend well beyond the mixing step and into downstream operations to multiply the benefits of reduced production time and labor costs.
2. Eliminate or simplify steps that don’t add value
When looking for ways to reduce costs at the mixing step, OEMs should evaluate the entire mixing process to identify, simplify and/or remove steps that add no value. Equipment cleanup steps, for example, are often overlooked as a process improvement opportunity. Cleanup is a requisite part of the mixing process in order to avoid contaminants or impurities in the blend. However, the cleanup process is notorious for consuming wasteful amounts of time and labor while adding zero value to mixing operations.
What if the cleanup step could be simplified or eliminated entirely? Most traditional mixer configurations involve complex mechanical agitators or moving parts that are difficult to clean post-mix and prone to contamination in subsequent mix batches. The RAM method of mixing, on the other hand, does not have internal mechanical components. This makes RAM mixers much easier and faster to clean and maintain while all but eliminating the possibility of contamination of subsequent mix batches. RAM can reduce or eliminate much of the cost and time required by traditional mixers to achieve desired hygiene and cleanliness levels, which consequently reduces labor and disposal costs, materials and cycle times.
3. Consider continuous operations
Another way to decrease labor costs is to move from batch processing to semi-continuous or fully-continuous mixing operations. Continuous processes typically rely more on automation that minimizes labor requirements. For OEMs that prefer to implement a semi-continuous process, one option involves the use of multiple, interchangeable mixing drums (mix vessels) with a single mixer to slice changeover times and improving efficiency.
For continuous operations, Resodyn’s Continuous Acoustic Mixer (CAM) system utilizes the identical advantages of the RAM mixing platform for high-throughput material mixing applications. In a continuous configuration, RAM technology utilizes a specially configured “tortured path” for materials. As the ingredients pass successively through stacked, inclined plains chambers, RAM Applies both vertical and acoustic energy to the materials in the entire stack, proceeding ingredients through the mixing stages.
RAM’s continuous stack configuration can transform a 144 kg per hour batch-mix into 432 kg per hour continuous mix.* Each CAM system delivers an environmentally-friendly Clean in Place (CIP) process that enables no-contact, no-disassembly cleaning, which greatly reduces the cost of labor otherwise required for cleanup of traditional mixers.
How RAM reduced labor costs in actual use
RAM technology is a reliable path to dramatic increases in quality and productivity while reducing processing challenges and time. Hundreds of companies and organizations across a dozens of industries prove RAM’s value. In the following two examples, this company benefited from improved capacity, competitiveness, and profitability once RAM technology was employed.
- The installation and use of a Resodyn RAM 5 system enabled an abrasives company to completely revamp its core mixing processes. In doing so, RAM simplified its processing design from five process steps and 53 mixing cycles to just two steps and three mixing cycles. Using actual customer data, the payback [period for this purchase was less than XX months.
- Traditional mixing technologies required the addition of a critical ingredient in very small doses for acceptable processing, amounting to 375 ingredient addition stepsper batch. RAM’s rapid incorporating effects reduced the addition steps to just five, which cut the ingredient addition labor from 3.5 hours to merely 2.5 minutes. RAM enabled a decrease in batch processing time from 10.5 hours to just 30 minutes, less than 5% of the time traditional mixing technologies were able to achieve.
About Resodyn Acoustic Mixers Inc.
From the world's top materials processing companies to international manufacturers, global tech giants, and nearly every U.S. National Laboratory, organizations in more than 30 countries rely on RAM’s single, powerful technology platform. Whether used for development of new materials in a laboratory or for running full-scale industrial production, RAM systems are available in configurations to fit applications across dozens of industries.
The Resodyn team works closely with its customers to mix virtually any combination of ingredients, including liquids, pastes, and powders. Whether nano-sized particles or pea-sized grains, highly viscous or thin liquids materials, RAM mixes them swiftly, efficiently and thoroughly. Resodyn products address a broad range of industrial mixing and processing challenges across the full spectrum of industrial sectors, including pharmaceuticals, chemicals, energy storage, electronics, energetics, polymers and ceramics.
Resodyn is the only company in the world to offer RAM technology. First hand witnessing of mixing and processing at a RAM demonstration, either online or on-site at your facility is always available, using your own materials, and solving your specific mixing challenges. Contact us today to schedule a demonstration and learn how RAM can help save time, reduce costs, boost quality, and bolster profitability.
* Batch mix at 36 kg per vessel, 5 minute mixing time, 10 minute changeover time or 4 batches per hour. Continuous Mix processes same 36 kg per 5 minutes, eliminating changeover time for 12 continuous cycles or 432 kg per hour.