

Home » Industries Served » Additive Manufacturing 3D Printing Processing | Powder Metals | Alloys | Polymers
THE 3D PRINTING AND ADDITIVE MANUFACTURING PROCESSING TECHNOLOGY OF CHOICE
Resodyn Acoustic Mixers, Inc. offers the best-in-class mixing/blending technology for manufacturers of metal, ceramic and polymer 3D printing materials for a range of additive manufacturing technologies.
RAM technology facilitates accelerated reaction times and homogenization processes to achieve superior flow properties for powders, enabling printing of complex geometries.
Increased dispersion rates, rapid emulsification and extended life suspensions promote efficiency, and reclamation can easily be attained without the need for additional equipment. Waste is significantly reduced and cycle time decreased, for improved production economics.
Applications for RAM products in the Additive Manufacturing (3D Printing) Industry are inclusive of:
- Alloys
- Ceramics
- Plastics
- Polymers
- Powder Metals
- Powder Metal Coatings
- Resins
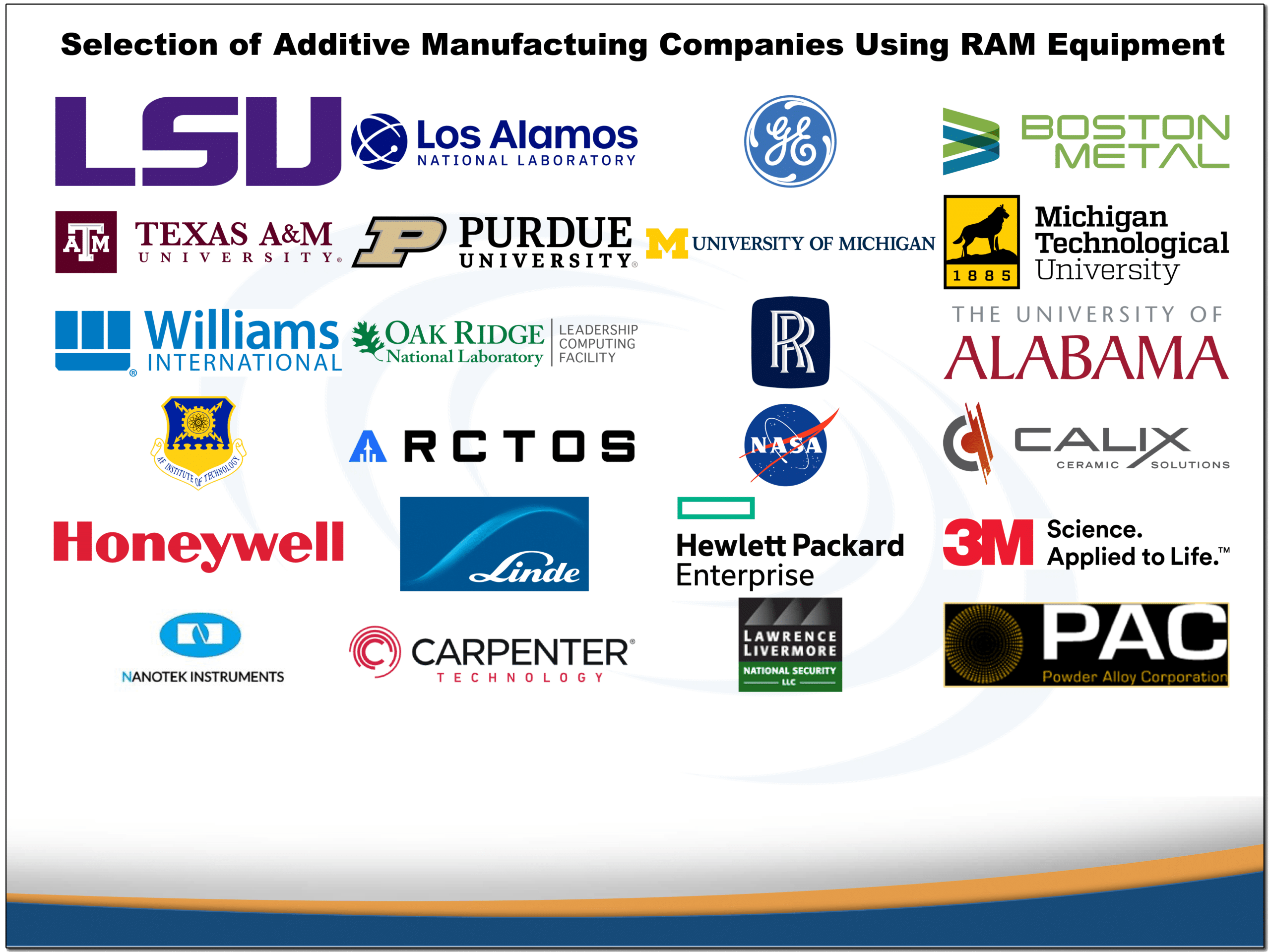
INDUSTRY EXPERT
TESTIMONIALS
“... [ResonantAcoustic® mixing] is a fantastic technology. It has revolutionized the way we mix for development of materials for additive manufacturing...”
- Nik Ninos, Research and Development Manager, Calix Ceramic Solutions
“…The LabRAM II has yielded some surprising and exciting results for us. We actually made a new metal alloy for additive manufacturing...”
- Research Scientist, U.S Government Agency
“… We were using reciprocal shakers to dissolve product we sampled off one of our production lines, and it was taking four hours just to prep the material for testing. Once we started using the LabRAM, it cut that time from four hours down to 20 minutes...”
- Lab Supervisor, U.S. Polymer Products Company
THE UNIVERSAL
MIXING SOLUTION
The ResonantAcoustic® Mixer (RAM) product line harnesses the power of resonance (low-frequency sound) to generate powerful and efficient mixing of complex Solid-Solid, Solid-Liquid, Liquid-Gas, and Liquid-Liquid Blends. Benefits include;
- 10-100X faster mixing times
- bladeless non-contact mixing
- consistent homogenization
- repeatable
- scalable
- durable
- custom engineered systems
- reliable
- cost saving
- eco-friendly operation
- unmatched safety
Videos on Mixing for Additive Manufacturing
NASA Invents GRX-810 SuperAlloy with RAM
NASA recently invented a new high temperature 3D-Printed GRX-810 superalloy with almost double the tensile strength, more than double the ductility, and orders of magnitude (10X-2000X) better creep rupture life than conventional superalloys and current 3D-printable metal parts.
GRX-810 cannot be produced by conventional machining, and is 3D-printed. GRX-810 can be used in space launch systems, heat exchangers in nuclear power plants and other extreme temperature environments, thanks to RAM technology.
GRX-810 is made by coating NiCoCr metal powder with a film of nanoscale Y2O3 oxide particles using RAM technology.
Prior attempts to mechanically alloy the Y2O3 onto the metal powder with traditional equipment had deformed the powder. It became more platelet-like, had a tendency to stick, and as a result was much more difficult to print.
RAM rapidly and powerfully, yet gently coats the metal powder with the ceramic, without deforming the powder. The powder remains very spherical and flows well through the 3D printer.
Dissimilar Powder Mixing in 10 Seconds!
Dry ingredients can be difficult to thoroughly and consistently mix, particularly when the particles are of different sizes and characteristics. To illustrate effective and rapid mixing, 10 grams of fumed silica is blended with 100 grams of sand. Completed specimens exhibit no airborne fumed silica, demonstrating uniform blending at an order of magnitude difference in particle size.
Milling and Nano Coating in 8 Seconds!
Coating larger particles with smaller ones is a common processing application, and milling is often a part of the same process. In this video, agglomerated carbon black particles are simultaneously milled to nano size particles that coat the plastic pellets completely in just a few seconds. The high speed video clearly illustrates the dispersion of carbon black particles, their de-agglomeration, and progressive and comprehensive coating of the plastic pellets.
Articles on Additive Manufacturing Mixing
Bi-modal particle size distribution for high energy product hybrid Nd–Fe–B—Sm–Fe–N bonded magnets
AIP Advances
“Homogeneity of the bonded magnet was accomplished by thoroughly mixing nylon and magnet powders using the LabRAM, Resodyn Acoustic Mixers prior to the compression molding. Mixing both components in powder form helped overcome the agglomeration difficulty during the magnetic field alignment process.”
Parmar, H., Paranthaman, M. P., & Nlebedim, I. C. (2024). Bi-modal particle size distribution for high energy product hybrid Nd–Fe–B—Sm–Fe–N bonded magnets. AIP Advances, 14(1). https://doi.org/10.1063/9.0000819
Fine-Tuning Collective Atomic Vibrations in Low-Dimensional Nanocarbon Multilayer Transition Interfaces for 3D Printed Extreme Lattice Metamaterials Performance Improvement
Material Processing
“We have developed a game-changing approach for additively manufactured extreme lattice metamaterials... . In particular, this chain includes combination of a set of techniques:... the resonant acoustic mixing of all nanocomponents, growing the high-end ELM elements by high-precision multi-material additive manufacturing as well as using the data-driven digital twins-based nanoscale manufacturing approach.”
Lukin, A. & Western-Caucasus Research Center. (2023). Fine-Tuning collective atomic vibrations in Low-Dimensional nanocarbon multilayer transition interfaces for 3D printed extreme lattice metamaterials performance improvement [Proceeding Paper]. Mater. Proc., x. https://sciforum.net/manuscripts/14530/manuscript.pdf
Facile manipulation of mechanical properties of Ti-6Al-4V through composition tailoring in laser powder bed fusion
Journal of Alloys and Compounds
“Plasma atomized Ti-6Al-4 V (Grade 23 with oxygen content no more than 0.13 wt%, 15–45 µm) and spherical CP Ti (Grade 1 with oxygen content no more than 0.18 wt%, 38–63 µm) were blended using resonant acoustic mixing.”
Du, X., Simonelli, M., Murray, J. W., & Clare, A. T. (2023). Facile manipulation of mechanical properties of Ti-6Al-4V through composition tailoring in laser powder bed fusion. Journal of Alloys and Compounds, 941, 169022. https://doi.org/10.1016/j.jallcom.2023.169022
Probing the role of solids loading and mix procedure on the properties of acoustically mixed materials for additive manufacturing
Powder Technology
“Resonant acoustic mixing has been of particular interest for use in additive manufacturing since viscous, solids-loaded materials can be difficult to mix and inhomogeneity has adverse effects on print quality. In this study, we detail a method to iterate through different formulations and mix procedures and assess mixture quality.”
Kline, D. J., Grapes, M. D., Avalos, E. A., Landeros, C. M., Martinez, H. P., Reeves, R. V., Sullivan, K. T., & Doorenbos, Z. D. (2022). Probing the role of solids loading and mix procedure on the properties of acoustically mixed materials for additive manufacturing. Powder Technology, 411, 117947. https://doi.org/10.1016/j.powtec.2022.117947
Apparent viscosity evolution law of trace RDX-based explosive ink in Resonance Acoustic-Mixing process
Journal of Materials Research/Pratt’s Guide to Venture Capital Sources
“To solve the problems of poor mixing consistency, low preparation efficiency and serious material waste of trace and high solid content explosive inks, this paper proposes a new preparation process by combining Resonant Acoustic-Mixing technology with rheological apparent viscosity... Under the best preparation process route, the ink could be prepared in only 5 min.”
Zhang, P., An, C., Mu, J., Cui, F., Cheng, W., Ye, B., & Wang, J. (2022). Apparent viscosity evolution law of trace RDX-based explosive ink in Resonance Acoustic-Mixing process. Journal of Materials Research/Pratt’s Guide to Venture Capital Sources, 37(17), 2793–2802. https://doi.org/10.1557/s43578-022-00669-0
3D-printed nanoporous ceramics: Tunable feedstock for direct ink write and projection microstereolithography
Materials & Design
“The 3YZ inks were made using solids loading in PEGDA ranging from 55 to 70 wt% (18–30 vol%, Table 2). The ink was mixed with spherical zirconia grinding beads (4mm diameter) in an acoustic mixer (LabRAM II, Resodyn Acoustic Mixers, Butte, MT) for 3h at 70 g-force to break up agglomerates and disperse the particles. The LabRAM II mixing time was determined by SEM images of the inks at different time points to ensure homogeneous dispersion... “
Troksa, A. L., Eshelman, H. V., Chandrasekaran, S., Rodriguez, N., Ruelas, S., Duoss, E. B., Kelly, J. P., Cerón, M. R., & Campbell, P. G. (2020). 3D-printed nanoporous ceramics: Tunable feedstock for direct ink write and projection microstereolithography. Materials & Design, 198, 109337. https://doi.org/10.1016/j.matdes.2020.109337
Cryomilled 17-4 Stainless Steel Powder as Feedstock for Additive Manufacturing
“…The blending process was carried out with a Resodyn LabRAM II
acoustic mixer operating for 1 h with 10 g’s of acceleration.”
Cryomilled 17-4 Stainless steel powder as feedstock for Additive Manufacturing - DSIAC. (2023, September 21). DSIAC. https://dsiac.dtic.mil/webinars/cryomilled-17-4-stainless-steel-powder-as-feedstock-for-additive-manufacturing/
Efficient production of a high-performance dispersion strengthened, multi-principal element alloy
Scientific Reports
“To produce AM material, equiatomic NiCoCr medium entropy alloy (MEA) powder which exhibited a diameter size range between 10–45 μm and Y2 O3 particles rated between 100–200 nm were acquired. A Resodyn LabRAM II ResonantAcoustic™ mixer was employed to coat the NiCoCr powder with one weight percent of nanoscale Y2O3...[the LabRAM II] quickly homogenized the powder, eventually coating the larger NiCoCr powder with a thin film of Y2 O3 after an hour of mixing in a polyurethane container...”
Smith, T. M., Thompson, A. C., Gabb, T. P., Bowman, C. L., & Kantzos, C. A. (2020b). Efficient production of a high-performance dispersion strengthened, multi-principal element alloy. Scientific Reports, 10(1). https://doi.org/10.1038/s41598-020-66436-5
Additive manufacturing of ammonium perchlorate composite propellant with high solids loadings
Proceedings of the Combustion Institute
“...20g batches of propellant were hand mixed in a 473 ml jar until
the AP was wetted. The mixture was then placed into a [Resodyn Acoustic Mixers LabRAM] resonant mixer. The HTPB binder propellant was mixed for 3 min at 80g for three repetitions with further hand mixing between cycles while the UV binder propellant was mixed in the Resodyn Acoustic Mixer for 2 min at 80g for 30s followed by a rest period of 30s...the techniques demonstrated in this paper could be used to create a wide range of complex grain structures that were not previously possible to manufacture.”
McClain, Gunduz, I., & Son, S. (2018). Additive manufacturing of ammonium perchlorate composite propellant with high solids loadings. Proceedings of the Combustion Institute, 37(3), 3135–3142. https://doi.org/10.1016/j.proci.2018.05.052
Additive Manufacturing of Carbon Fiber Reinforced Silicon Carbide Solid Rocket Nozzles
AIAA SCITECH 2022 Forum
“Suitable green body formulations were developed and tested prior to being printed. The final formulation was viscous enough to hold its shape during the 3D printing process so there was minimal deformation before the part was thermoset. 40 g batches were made in a Resodyn ResonantAcoustic™ mixer for three cycles of 3 minutes at 80g. The properties of the mixture did not vary over the course of a few days, making it printable within that time frame.”
McClain, M. S., Gunduz, I. E., & Son, S. F. (2019). Additive manufacturing of carbon fiber reinforced silicon carbide solid rocket nozzles. AIAA SCITECH 2022 Forum. https://doi.org/10.2514/6.2019-0408
Resonant Acoustic® Mixing: Processing and Safety
Propellants Explosives Pyrotechnics
“New processing technologies are allowing researchers, industry and academia to probe new materials space not previously achievable. These technologies include additive manufacturing and Resonant Acoustic® Mixing (RAM), both of which have expanded in their use and application over the last 15–20 years.”
Andrews, M. R., Collet, C., Wolff, A., & Hollands, C. (2019). Resonant Acoustic® Mixing: Processing and safety. Propellants Explosives Pyrotechnics, 45(1), 77–86. https://doi.org/10.1002/prep.201900280
Environmentally Friendly Boron-Based Pyrotechnic Delays: An Additive Manufacturing Approach
ACS Sustainable Chemistry & Engineering
“The three reactive systems were formulated with an equivalent amount of dry powder Methocel using a Resodyn LabRAM mixer and same method as the dry powder mixtures that did not contain Methocel.”
Walters, I. T., & Groven, L. J. (2019). Environmentally Friendly Boron-Based Pyrotechnic Delays: an additive manufacturing approach. ACS Sustainable Chemistry & Engineering, 7(4), 4360–4367. https://doi.org/10.1021/acssuschemeng.8b06204
Two-component additive manufacturing of nanothermite structures via reactive inkjet printing
Journal of Applied Physics
“…a pre-mixed aluminum copper (II) oxide suspension was mixed at a 6% volumetric solid loading. 15 To prepare the material, nCuO was mixed with nAl and suspended in a solution of DMF and PVP and placed in a 10ml syringe (BD, slip tip). The syringe was loaded into a custom polytetrafluoroethylene (PTFE) holder and secured on a LabRAM ResonantAcoustic™ Mixer. The syringe was mixed at 80% intensity for 16 min and inverted after 8 min.”
Murray, A. K., Isik, T., Ortalan, V., Gunduz, I. E., Son, S. F., Chiu, G. T., & Rhoads, J. F. (2017). Two-component additive manufacturing of nanothermite structures via reactive inkjet printing. Journal of Applied Physics, 122(18). https://doi.org/10.1063/1.4999800
Printed Energetics
CRC Press eBooks
“…it was shown that by using a Resodyn LabRAM mixer, the nanothermite could be processed directly within the deposition.”
Pramanik, B. (2017). Dynamic characterization of energetic materials. In CRC Press eBooks (pp. 87–93). https://doi.org/10.1201/9781315166865-7
Relevant Patents on Additive Manufacturing Mixing
Approved and pending applications for work involving additive manufacturing and the use of ResonantAcoustic® mixing technology as the
preferred embodiment.
Conditioned metal particles for three-dimensional printing
WO WO2023282912A1 David R. Otis, Jr., Vladek Kasperchik & Mohammed Shaarawi Priority 2021-07-09 • Filed 2021-07-09 • Published 2023-01-12
Methods of preparing a particulate build material for three-dimensional printing can include loading fresh particulate build material including from about 80 wt% to 100 wt% fresh metal particles into a mechanical mixer, and mechanically conditioning the fresh particulate build material to generate conditioned particulate build material including conditioned metal particles. The fresh metal particles can have a surface oxide layer, and the fresh particulate build material can have a particle size distribution with a D10 particle size from about 2 µm to about 10 µm, a D50 particle size from about 5 µm to about 20 µm, and a D90 particle size from about 20 µm to about 40 µm. The conditioned particulate build material can include a modified cohesive index (compared to the fresh conditioned particulate build material) ranging from about 25 cohesive index units to about 35 cohesive index units.
Highlighted Use: A LabRAM II conditioned metal particles.
Porous ceramics for additive manufacturing, filtration, and membrane applications
WO US US20230219058A1 Patrick Campbell, Sarah Baker, Maira R. Ceron Hernandez, Jennifer Marie Knipe & Joshuah K. Stolaroff Lawrence Livermore National Security, Llc
Priority 2017-06-23 • Filed 2023-03-22 • Published 2023-07-13
An ink for three dimensional printing a ceramic material includes metal oxide nanoparticles and a polymer resin, where a concentration of the metal oxide nanoparticles is at least about 50 wt % of a total mass of the ink. A method of forming a porous ceramic material includes obtaining an ink, where the ink comprises a mixture of metal oxide nanoparticles and a polymer, forming a body from the ink, curing the formed body, heating the formed body for removing the polymer and for forming a porous ceramic material from the metal oxide nanoparticles. The forming the
body includes an additive manufacturing process with the ink.
Highlighted Use: RAM equipment mixes nanoparticles in a polymer resin.
Spherical microparticles formed using emulsions and applications of said microparticles
US US20210347701A1 James Timothy Cahill, Wyatt Du Frane, Joshua D. Kuntz, Ryan Lu, Amy Wat, Marcus A. Worsley & Congwang Ye Lawrence Livermore National Security, LLC
Priority 2020-05-08 • Filed 2021-05-07 • Published 2021-11-11
A composition includes a plurality of microparticles, where the microparticles comprise agglomerates of nanopowder, wherein the nanopowder includes a material selected from the following: a ceramic material, a metal, an alloy, a polymer, or a combination thereof. The microparticles are characterized by having an essentially spherical shape, nanograin features substantially identical to nanograin features of the nanopowder prior to formation into the microparticles, and a nanoscale porosity defined by the nanograin features. The plurality of microparticles have an essentially uniform size relative to one another. Moreover, the composition has flowability having a Hausner Ratio representing tapped density: bulk density less than 1.25.
Highlighted Use: RAM mixers combine a blend of metal and ceramic with solvent and additives.
A Ceramic Reinforced Metal Composite For Hermetic Bodies For Implantable Devices
EP US US20230085958A1 Christine A. Frysz, Dallas J. Rensel, Brian P. Hohl, Jonathan Calarnel & Xiaohong Tang Greatbatch Ltd.
Priority 2021-09-10 • Filed 2022-09-12 • Published 2023-03-23
A ceramic reinforced metal composite (CRMC) comprising a composition composite as an interpenetrating network of at least two interconnected composites is described. The interpenetrating networks comprise a ceramic matrix composite (CMC) and a metal matrix composite (MMC). The composition composite is particularly useful as an electrically conductive pathway extending through the ceramic body of a hermetically sealed component, for example, a feedthrough in an active implantable medical device (AIMD).
Highlighted Use: RAM mixers combine a blend of metal and ceramic with solvent and additives.
Reducing surface roughness of cured three-dimensional printed objects using a localized heat source
WO WO2023101682A1 Emre Hiro Discekici, Shannon Reuben Woodruff, Alay Yemane & Greg Scott Long
Hewlett-Packard Development Company, L.P.
Priority 2021-12-03 • Filed 2021-12-03 • Published 2023-06-08
Examples of the present disclosure are directed toward methods and system for reducing surface roughness of a cured three-dimensional (3D) printed object using a localized heat source. An example method includes applying a liquid solvent to the cured 3D printed object and heating the cured 3D printed object with the liquid solvent applied thereto to a temperature below a melting point of the cured 3D printed object using a localized heat source to reduce a surface roughness of the cured 3D printed object as compared to the cured 3D printed object prior to
the application of heat.
Highlighted Use: RAM mixers combine solvent types.
Kit for three-dimensional printing
WO WO2023101688A1 Emre Hiro Discekici, Emily Levin & Jake Thomas Filed 2021-12-03 • Priority 2021-12-03 • Published 2023-06-08
A kit for three-dimensional (3D) printing is described. The kit comprises a build material composition; a fusing agent composition including a radiation absorber present in an amount ranging from about 0.01 wt % to about 2.0 wt % of a total weight of the fusing agent composition, wherein the radiation absorber absorbs radiation at a wavelength range within the visible light spectrum; and a fusing assist composition including a first co-solvent; a second co-solvent; and a balance of water.
Highlighted Use: RAM mixers create the fusing agent used.
WO WO2023101683A1 Emre Hiro Discekici, Emily Levin & Jake H. Thomas
Filed 2021-12-03 • Priority 2021-12-03 • Published 2023-06-08
Examples of the present disclosure are directed toward fusing agent compositions. An example fusing agent composition includes a radiation absorber, a co-solvent mixture, and a balance of water. In various examples, the radiation absorber is present in an amount ranging from about 0.005 weight percent (wt %) to about 1.0 wt % of a total weight of the fusing agent composition, wherein the radiation absorber absorbs radiation at a wavelength range within the visible light spectrum.
Highlighted Use: RAM mixers create the fusing agent used.
Method of abrading a workpiece
WO WO202202384A1 Polly H. R. Keen
Filed 2021-07-08 • 2022-02-03
A method of abrading a surface of a workpiece comprises providing a vessel containing loose abrasive bodies, loose resilient foam bodies, and at least a portion of the workpiece. At least most of the loose abrasive bodies have a maximum dimension of 3 centimeters. At least most of the loose abrasive bodies have a maximum dimension of 0.1 to 3 centimeters. The vessel is then agitated with sufficient energy such that at least some of the loose abrasive bodies contact and abrade at least a portion of the surface of the workpiece.
Highlighted Use: A RAM mixer works with abrasives and foam bodies.
Method of finishing a workpiece and finishing vessel having deflecting element
WO WO2021205399A1 Polly H. R. Keen, Andrew R. Henry & Jonathan J. O’Hare
Filed 2021-04-09 • Published 2021-10-14
A method of finishing a surface comprises vibrating a finishing vessel in a reciprocating linear manner. The finishing vessel contains working bodies and a workpiece. The finishing vessel includes a processing chamber that has at least one deflecting element. A finishing vessel suitable for use in the method is also disclosed.
Highlighted Use: A RAM mixer provides the force to finish the surface of a part.
Loose abrasive bodies and method of abrading a workpiece using the same
WO US WO2021156730A1 Polly H. R. Keen & Helen E. Pearson 3M Innovative Properties Company
Priority 2020-02-06 • Filed 2021-02-01 • Published 2021-08-12
A method of abrading a surface of a workpiece comprises agitating a vessel containing loose abrasive bodies and the workpiece. At least most of the loose abrasive bodies have a maximum dimension of 0.25 to 3 centimeters. On a respective basis, each loose abrasive body comprises abrasive particles secured to an organic substrate by a binder material. The vessel is agitated with sufficient energy such that at least some of the loose abrasive bodies contact and abrade at least a portion of the surface of the workpiece. A plurality of chopped loose abrasive bodies, wherein, on a respective basis, the chopped loose abrasive bodies each comprise abrasive particles secured to a substrate and have a maximum dimension of 0.25 to 1.5 centimeters is also disclosed.
Highlighted Use: A LabRAM mixer used discarded materials as a superior abrasive to loose particles.
Chemical-free fabrication of graphene reinforced polymer matrix composites
WO US CN JP KR JP7170537B2 Aruna Tsar & Bor Z Jang
Priority 2015-12-10 • Filed 2016-12-07 • Granted 2022-11-14 • Published 2022-11-14
A simple, rapid, scalable, environmentally friendly method of directly producing graphene reinforced polymer matrix composites from graphitic materials: (a) a plurality of graphitic materials in a collision chamber of an energy collision device. Mixing a plurality of particles of the solid polymer support material to form a mixture; (b) exfoliating the graphene sheet from the graphite material and transferring the graphene sheet to the surface of the solid polymer support material particles Operating the energy collision device with a frequency and intensity for a time sufficient to form graphene coated polymer particles or graphene embedded polymer particles inside the collision chamber; (c) graphene coated polymer particles or graphene-reinforced polymer matrix composite
from embedded polymer particles Method comprising the steps of forming is provided. Also provided are materials of graphene coated polymer particles or graphene embedded polymer particles produced by this method.
Highlighted Use: A RAM mixer created graphene from ABS pellets and expanded graphite.
WO US EP WO2020222747A1 Emre Hiro Discekici, Shannon Reubern Woodruff & Carolin Fleischmann
Filed 2019-04-29 • Priority 2019-04-29 • Published 2020-11-05
An example of a build material composition for three-dimensional (3D) printing includes a polyamide material and an antioxidant. The antioxidant consists of an aromatic multihydrazide; or an aromatic sulfonomonohydrazide; or a hydrazide having formula (I) disclosed herein, wherein: R is null, a C1 to C12 unbranched alkyl, a C3 to C8 branched alkyl, a C2 to C8 unbranched alkylene, a C4 to C8 branched alkylene, an alicyclic compound, a polyethylene glycol, or a combination thereof; A is C=O, O=S=O, P=O, or C=S; and n is an integer ranging from 1 to 4; or formula (II) disclosed herein wherein A is C=O, O=S=O, P=O, or C=S.
Highlighted Use: A RAM mixer created a 3D build material from nine different dihydrazides.
Method for resonant-vibratory mixing
US US7866878B2 Harold W. Howe, Jeremiah J. Warriner, Aaron M. Cook, Scott L. Coguill & Lawrence C. Farrar Resodyn Acoustic Mixers
Filed 2007-01-10 • Priority 2007-01-10 • Published 2011-01-11
A method for mixing fluids and/or solids in a manner that can be varied from maintaining the integrity of fragile molecular and biological materials in the mixing vessel to homogenizing heavy aggregate material by supplying large amounts of energy. Variation in the manner of mixing is accomplished using an electronic controller to generate signals to control the frequency and amplitude of the motor(s), which drive an unbalanced shaft assembly to produce a linear vibratory motion. The motor may be a stepper motor, a linear motor or a DC continuous
motor. By placing a sensor on the mixing vessel platform to provide feedback control of the mixing motor, the characteristics of agitation in the fluid or solid can be adjusted to optimize the degree of mixing and produce a high quality mixant.
Highlighted Use: RAM technology can mix a variety of materials.
Apparatus and method for resonant-vibratory mixing
US US7188993B1 Harold W. Howe, Jeremiah J. Warriner, Aaron M. Cook, Scott L. Coguill & Lawrence C.
Farrar Resodyn Acoustic Mixers
Filed 2004-01-26 • Priority 2004-01-26 • Published 2007-03-13
An apparatus and method for mixing fluids and/or solids in a manner that can be varied from maintaining the integrity of fragile molecular and biological materials in the mixing vessel to homogenizing heavy aggregate material by supplying large amounts of energy. Variation in the manner of mixing is accomplished using an electronic controller to generate signals to control the frequency and amplitude of the motor(s), which drive an unbalanced shaft assembly to produce a linear vibratory motion. The motor may be a stepper motors a linear motor or a DC continuous motor. By placing a sensor on the mixing vessel platform to provide feedback control of the mixing motor, the characteristics of agitation in the fluid or solid can be adjusted to optimize the degree of mixing and produce a high quality mixant.
Highlighted Use: RAM technology can mix a variety of materials.
US WO EP US10835880B2 Peter Andrew Lucon & Zachary Ruprecht Martineau Resodyn Corp.
Filed 2017-09-05 • Priority 2017-09-05 • Published 2020-11-17
A system for continuously processing a combination of materials includes a continuous process vessel having an outlet and one or more inlets. The continuous process vessel is configured to oscillate along an oscillation axis. An acoustic agitator is coupled to the continuous process vessel. The acoustic agitator is configured to oscillate the continuous process vessel along the oscillation axis. An outlet passage is in fluid communication with the outlet. At least a portion of the outlet passage or at least a portion of the continuous process vessel is disposed within a portion of the acoustic agitator.
Highlighted Use: RAM equipment can mix for long durations.
Additive Manufacturing Mixing Folio
Industry Folio
Three types of materials account for most of what is used in industrial additive manufacturing: polymers, ceramics and metals. While polymers are the most commonly used, certain additive techniques make use of specific materials as well as the unique capabilities of RAM technology. These materials are most often produced in either powder form or as wire feedstock.
Download this folio of insightful testimonials and links to informative technical papers, articles and patents involving RAM’s impact on the development and use of additive manufacturing materials.
ADDITIVE MANUFACTURING
MIXERS FOR 3D PRINTING
LabRAM II
1,000 gram capacity for repetitive and small sample processing
Up to 2.2 lb (1,000 gram) payload capacity full-featured, digitally controlled batch mixer for bench-scale development, mixing, and processing.
OmniRAM
5 kg capacity delivers pilot and small-scale development capabilities
11 lb (5 kg) payload capacity, full featured, digitally controlled batch mixer for larger-than-bench-scale development, pilot and small-scale production and processing.
Continuous Acoustic Mixer (CAM)
High throughput mixing for pilot and production scale
Continuous Acoustic Mixing (CAM) systems are configurable for OmniRAM, RAM 5, and RAM 55. CAM systems are custom built for the application and enable high-throughput acoustic mixing of powders, pastes, and liquids.