Mix Diverse Battery Material
Accurately and Consistently
With Breathtaking Speed
ResonantAcoustic® Mixers (RAM) deliver cutting-edge performance for the battery industry, offering unmatched speed and efficiency in mixing advanced materials like solid-state battery components and nanocomposites. These battery mixers ensure precise, consistent results while minimizing solvent use and optimizing production processes.
Key RAM advantages:
- 144x faster processing of electrode slurries
- Ideal for solid-state battery materials mixing and nanocomposites
- Uniform mixing of materials with varied sizes, densities, and shapes
- Reduced solvent usage in solid/liquid mixtures
- Rapid application of conductive coatings like carbon
“... RAM gives us a QUICK, EASY, AND CONVENIENT method
of mixing in a single unit...”
- Global Energy Storage Products Company
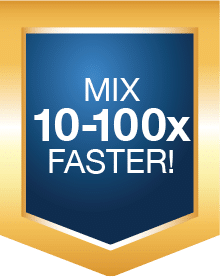
RAM Mixers: Setting the Bar for Battery
Manufacturing
Our industrial batch mixers and continuous mixers streamline the production of batteries by providing fast, highly repeatable batch mixing processes.
Whether you’re a battery manufacturer or involved in high-energy-density material blending, our equipment offers superior ingredient distribution, minimal cleanup, and scalability from lab-scale mixing to full-scale industrial production. This makes us the preferred choice globally for companies involved in the manufacturing of batteries and energy storage systems.
Extremely fast: Mixing times have been reduced from hours to minutes.
Powder mixing: Materials of different bulk densities, sizes, and morphologies are easily mixed.
Slurry mixing: RAM technology performs wetting, incorporation, and mixing steps consistently.
Superior quality: Ensures better mix performance with highly repeatable results.
Minimal cleanup: No blades, impellers, or other internal hardware to clean up.
“... Mixing was taking six hours on a planetary mixer. With RAM, mixing and milling is accomplished as one process that takes only 2-3 minutes...”
- U.S. East Coast Battery Manufacturer
Loaded polymer blending:
Two materials of very different particle sizes are blended with a polymer surrogate to illustrate a heavily loaded polymer blend.
Starting viscosity: 2,100 cP
Ending viscosity: 350,000 cP
Ready to see it for yourself?
Why Resodyn?
Fast-track battery development with the power of resonance
RAM battery mixers provide exceptionally thorough mixing at breathtaking speed, accelerating your battery research and development efforts, reducing time, complexity, and cost.
Our industrial chemical mixers ensure consistency and efficiency across all stages of battery development, from initial research to full-scale production.
Unmatched Performance
RAM products are bladeless and support a range of mixing needs. Pastes, gels, and powders of different bulk densities, sizes, and morphologies are easily mixed and evenly dispersed.
RAM excels at mixing:
- Aluminum oxide-filled silicone gels
- Battery pastes and slurries
- Copper pastes
- Encapsulation materials
- Epoxy insulators
- Ferrite compounds
Scale From Bench to Industrial with Confidence
ResonantAcoustic® Mixing mixes virtually any combination of materials at scales ranging from bench development to industrial production.
Our single, powerful technology platform is trusted by the world’s top materials companies from international pharmaceutical and biotechnology manufacturers to global battery tech giants.
Whether you’re developing new materials in the laboratory or running full-scale industrial production, RAM systems are available in configurations to fit your application.
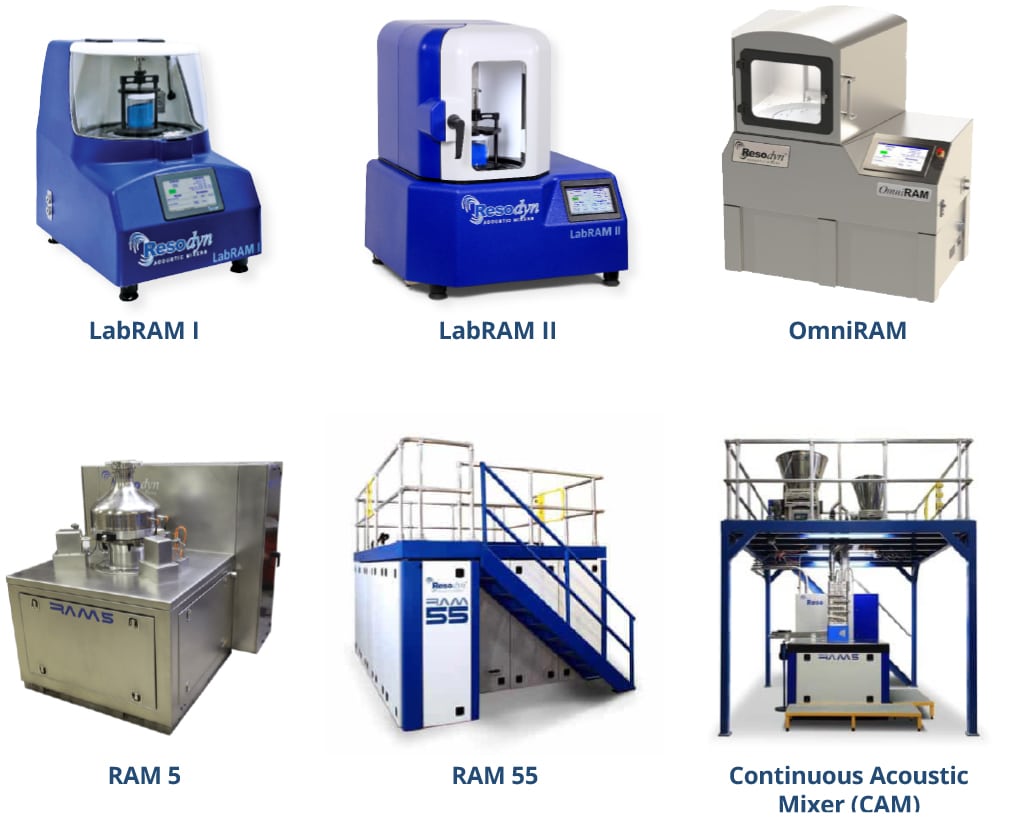
Out-Mix the Competition
- ResonantAcoustic Mixer
- V-Blender
- Paddle or Ribbon Blender
- Planetary Mixers
Mixing MechanismDiffusion MixingConvective MixingDe-mixing
Uses up to 100 g to drive random particle motion to mix.Uses vessel movement at 60 Hz (~3,600 cycles per minute) to impart high energy chaotic motion.Random and chaotic motion of RAM prevents de-mixing.
Uses gravity (1 g) as the restoring force to drive small scale random particle motion.Uses rotational movement at ~30 rpm to split and combine material systematically.The systematic motion of the v-blender can cause de-mixing.
Diffusion mixing is only a supplementary process for smaller particles and over longer mixing times.Uses an impeller of some type to move particles from one location to another within the powder bed.
Some mixers have increased impeller speeds which will impart shear mixing to break down agglomerates.
If there is a difference in particle sizes, larger particles tend to settle at the bottom.
Particles with different densities can separate over time.
Overloading can reduce mixing efficiency and increase the risk of de-mixing.
Planetary mixers mix by mechanical means, rather than diffusion.The rotating bowl and planetary motion create
a circular flow of the ingredients, causing them to mix through convection.Viscosity differences: If the ingredients have different viscosities, the mixer may not be able to maintain a homogeneous mixture. The higher-viscosity components can settle to the bottom while the lower-viscosity components remain on top.
Particle size differences: If the particles in the mixture have different sizes, they can also separate. Larger particles may settle to
the bottom while smaller particles remain suspended.Density differences: Ingredients with different densities can also de-mix. The denser components may settle to the bottom, due to gravity.
Case Study:
Revolutionizing lithium battery production with advanced mixing technologies
The experiments demonstrated in the Lithium-ion Battery Manufacture White Paper showcase that the ResonantAcoustic® mixing process is rapid, requiring less than one minute mixing time compared to six hours that is typically necessary to mix the product used in the formation of Li-ion battery electrodes. Our battery material blending equipment is transforming lithium-ion battery production.
Post-mix analysis showed that the mixture was very uniform, fully meeting the product specification. Moreover, this complex mix formulation demonstrated that the RAM technology was capable of powder-powder mixing, powder coating, and powder-resin blending without the need for any system modification.
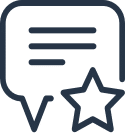
Client Testimonial
“We achieved a cathode with a higher specific capacity and improved rate performance because of the minimal side reactions at the cathode−solid electrolyte interface. These results demonstrate the success of the ResonantAcoustic® coating of NiCo2S4 NPs on NCM 622.”
-Young-Jin Kim, et al.
ACS Omega 2021
Experience the power of RAM firsthand with our expert team
Our sales professionals offer high-impact, on-site product demonstrations and personalized mixing tests using your materials — all at no cost to you. Discover the difference Resodyn can make for your operations today.
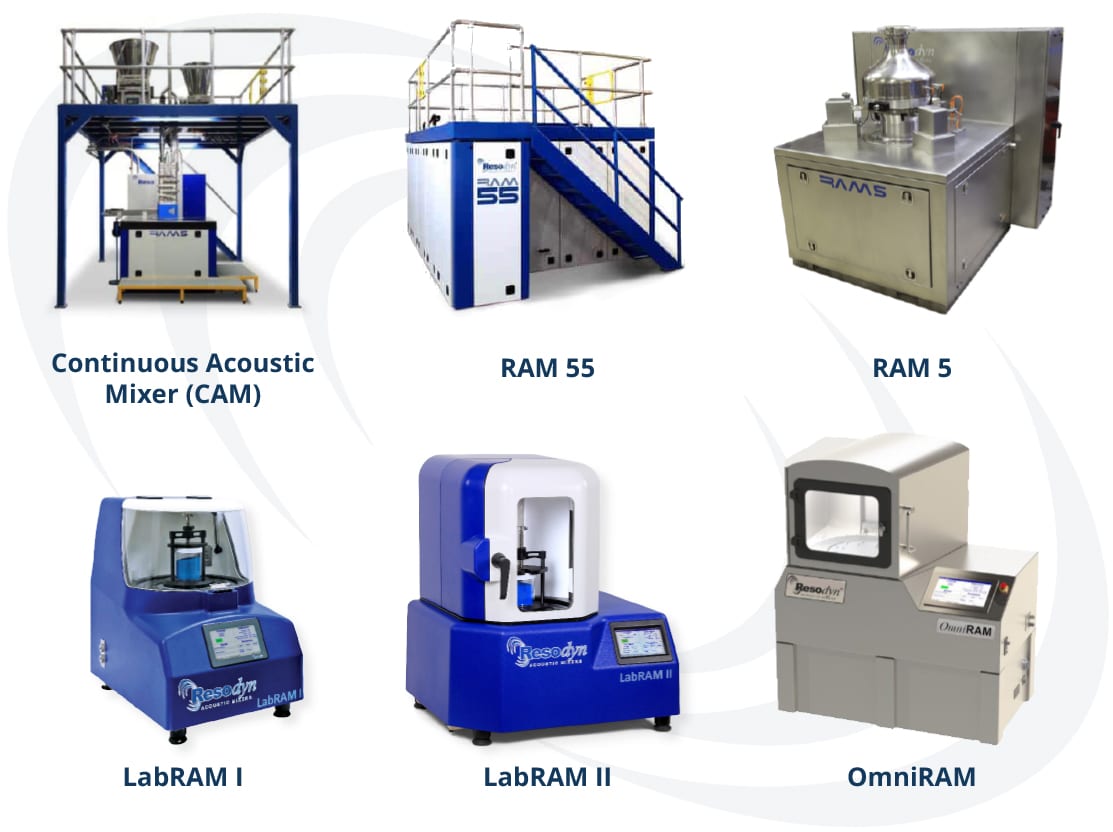
RAM Battery Mixers
Our industry-specific ResonantAcoustic® Mixers are the battery and energy storage processing technology of choice. We have models to scale with your business, ensuring consistent efficiency from clinical trial to full-scale production.
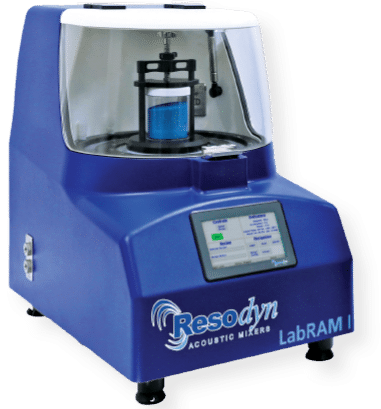
LabRAM I
Capacity: Up to 0.7 lb (300 g)
1.1 lb (500 g) payload capacity, full- featured, digitally controlled batch mixer for bench scale development without sacrificing features or power.
- Easy-to-use controls
- Low, medium, and high (40, 60, and 80 g) mixing Acceleration Settings
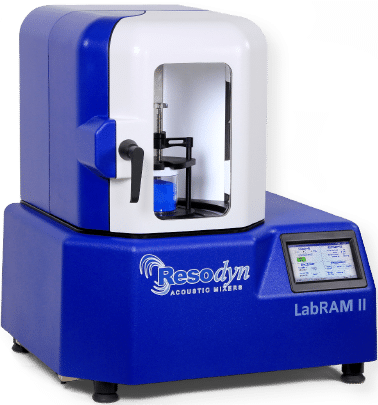
LabRAM II
Capacity: Up to 2.2 lb (1,000 g)
Up to 2.2 lb (1,000 g) payload capacity full-featured, digitally controlled batch mixer for bench-scale development, mixing, and processing.
- Touch screen interface
- Onboard operating system for real-time monitoring, recipe storage, and data retention
- Scales easily from development to production without additional testing
- Mix at vacuum or pressure
- Vacuum and temperature measurement/ control are available with a jacketed vessel system
- 0-100 g of powerful acceleration (100x the acceleration of gravity) at approximately 60 Hz (3600 RPM)
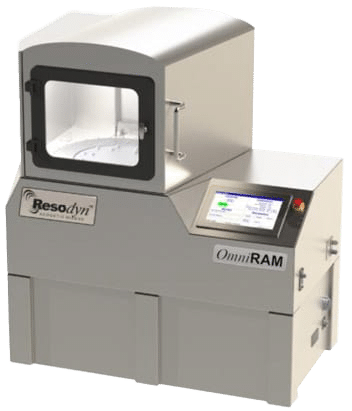
OmniRAM
Capacity: Up to 11 lb (5 kg)
11 lb (5 kg) payload capacity, full-featured, digitally controlled batch mixer for larger- than-bench-scale development, pilot and small-scale production and processing.
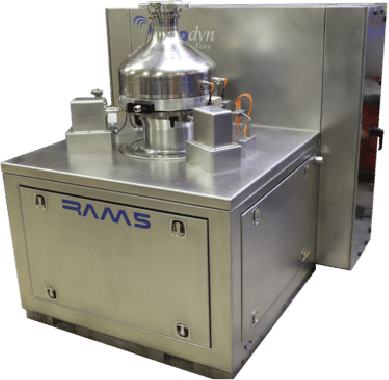
RAM 5
Capacity: Up to 80 lb (36 kg)
80 lb (36 kg) payload capacity, digitally controlled, batch mixer with multiple processing capabilities and options for pilot production and processing.
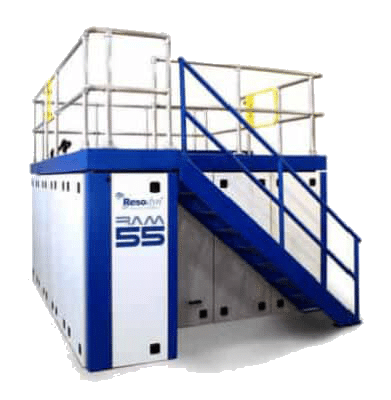
RAM 55
Capacity: Up to 924 lb (420 kg)
With a batch payload capacity of up to 924 lbs (420 kg) RAM 55’s digitally controlled, multiple processing capabilities multiply RAM’s value through direct and easy scale-up from bench development to large-scale batch production.
Key features for all pilot and production scale models:
- 0-100 g powerful acceleration (100x the acceleration of gravity) at approximately 60 Hz (3600 RPM)
- Consistent acceleration capability at the same amplitude, provides the continuity that makes scale-up a breeze.
- Configurable for continuous production
- Advanced and customizable mix vessel and enclosure designs are available to meet client requirements
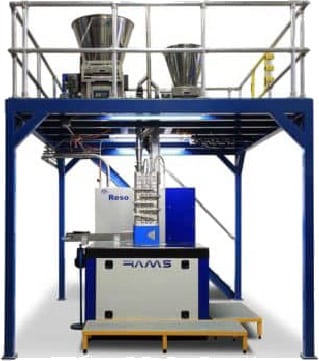
Continuous Acoustic Mixer (CAM)
Capacity: Dependent upon model
Continuous Acoustic Mixing (CAM) systems are configurable for OmniRAM, RAM 5, and RAM 55. CAM systems are custom-built for the application and enable high-throughput acoustic mixing of powders, pastes, and liquids.
Configurable for:
- OmniRAM
- RAM 5
- RAM 55
- Customizable for specific applications
- Suitable for a wide range of materials
- 0-100 g powerful acceleration (100x the acceleration of gravity) at approximately 60 Hz (3600 RPM)
- Consistent acceleration capability at the same amplitude, provides the continuity that makes scale-up a breeze.
Take the Next Step!
406.497.5333Demonstration
Schedule a free demo with our expert team at your facility or ours and see our mixers in action.
Mix test
From basic mixing tests to advanced formulation and scale-up, our experts will help you find the perfect protocol.
Price quote
Get a personalized quote and answers to all your questions to find the ideal RAM model for your needs.
Prefer to email? Contact us at:
info@resodynmixers.com
We’re excited to hear from you!
*Required field
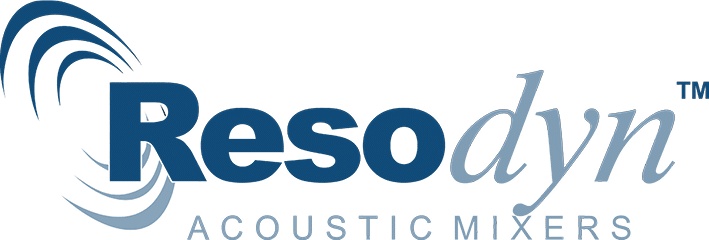
Resodyn Acoustic Mixers
130 North Main Street, Suite 630
Butte, MT, 59701
© 2024 Resodyn Acoustic Mixers, Inc