Home » Applications » High Viscosity Mixers
RAM EASILY MIXES HIGHLY VISCOUS MATERIALS & PASTES THAT OTHER MIXERS CAN’T
Viscosity is a measure of how resistant a fluid is to flow and is measured in centipoise (cP) and is one of the properties that influences how easily a mixture can achieve homogeneity.
Low viscosity materials - such as water, have a lower resistance and flow more rapidly. Water has a viscosity of 1 cP.
High viscosity materials - such as honey or tar resist deformation and flow more slowly. honey has a viscosity ranging from 2,000 to 10,000 cP. Some highly viscous materials have a viscosity of hundreds of millions centipoise.
Pastes and highly viscous mixes are made up of solids in a liquid matrix. Less liquid in the matrix produces higher viscosity, into the hundreds of millions of centipoise – approaching what appears to be and behaves much like a solid.
Finding a high viscosity mixer that works fast and mixes evenly is nearly an impossible thing to find... until now.
Resonant Acoustic Mixing (RAM) easily mixes highly viscous materials at speeds and uniformity that no traditional mechanical mixer comes close too. Using sound energy, RAM mixers deliver wetting, incorporation, and widespread mixing rapidly and uniformly throughout the matrix.
RAM mixers accelerate these processes by inducing Faraday Instabilities, or invasive “fingers” coupled with enveloping “cavities” at the boundary between materials of different densities. Progressing rapidly through wetting, incorporation, and mixing, RAM delivers highly homogeneous, higher viscosity results significantly faster than traditional technologies.
Overcome Mechanical Restrictions
Traditional, blade and axis technologies can work through early stages of wetting and possibly incorporation, but often overheat or grind to a halt when mixing starts and the viscosity increases.
Every highly viscous mixing process requires wetting, incorporation, and mixing phases. Without the mechanical limitations of axis/blade methods that require all materials to pass through a limited mixing zone, RAM technology performs all three steps simultaneously and consistently throughout the mixing vessel, reducing processing time by orders of magnitude.
Low Shear Mixing Regardless of Viscosity
RAM technology is a “non-contact” mixing method requiring no blades, propellers, or other engineered devices to cause mixing. This also means that the high shear traditionally associated with viscous materials can be eliminated, allowing delicate or hazardous materials to be processed rapidly without excessive heat build-up or physical shear stress.
Rapidly Achieve High Viscosity Mixing Uniformity
The more viscous a material, the more difficult it is to mix traditionally. This means that consistent dispersion and distribution suffer at higher centipoise. These restrictive phenomena are completely avoided using RAM mixers at any scale.
Sound energy wets, incorporates, and mixes materials rapidly, thoroughly and at levels of quality not previously possible. Over years of test data across numerous industrial installations, RAM devices have delivered exceptional results, well into the tens of millions of centipoise.
High Viscosity Mixing and Processing Accessories
Every RAM device’s mixing parameter variables can be enhanced by combinations of vacuum, mixing payload temperature control, and other accessories. Viscous materials often mix more effectively at higher temperatures and under vacuum. RAM systems provide these functions before, during, and after actual mixing operations. This means that idle, degassing time, and failed batches due to the wrong temperature are eliminated.
HOW RAM HIGH VISCOSITY MIXERS
DELIVER RESULTS 10x - 100x FASTER
The Mechanics of RAM Mixing
RAM's high viscosity mixer drives intense liquid to particle interaction at the wetting stage of viscous ingredient processing through Faraday Instabilities, throughout the materials instantly and continuously.
After incorporation, RAM’s sound energy enables mixing at high viscosities. Without restrictions of mechanical mixing methods and the heat and sheer they generate, RAM allows highly viscous materials to be mixed at the densest levels.
- Vertical vessel movement of 60 x/second and 0.55” / 14 mm displacement, at up to 100 g of acceleration generates intense particle motion
- RAM’s primary viscous mixing mechanism is intense liquid and solids material boundary interaction, and highly effective sound energy facilitating and accelerating mixing.
- The addition of processing vacuum or temperature improves many viscous ingredient mixes and aids in degassing
HOW RAM MIXERS COMPARE TO
TRADITIONAL HIGH VISCOSITY MIXERS
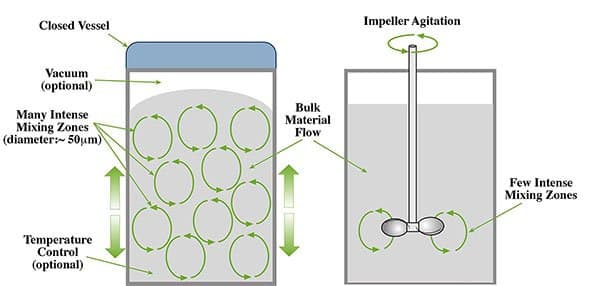
Stop Excessive Heat and Shear
- Traditional high viscosity mixing methods require all ingredients to traverse the entire vessel to repeatedly enter and exit a small, mechanically driven mixing area to achieve proper mixedness.
- Viscous materials experience high temperature generation and physical shear, damaging many ingredients. RAM technology activates all ingredients throughout the vessel immediately, eliminating material motion without mixing. RAM mixes everywhere in the vessel without mechanical devices or accessories, reducing temperature generation and eliminating physical shear.
Bringing Quality to High cP Processing
- High quality viscous performance requires thorough distribution of solids in the liquid matrix, for consistent processing characteristics at any place in the final product.
- RAM’s intense and pervasive processing facilitates solid particle separation and dispersion, improving dispersion, consistency, and performance.
WATCH TO LEARN ABOUT RAM
HIGH VISCOSITY MIXING
Rocket Motor Static Fire: Composite Propellant made with RAM by The Falcon Project LTD UK
Static fire of a 49 kg composite propellant rocket motor made with RAM:
Boost - Sustained Thrust Profile
Loaded Polymer Blending in Less than 3 Minutes!
To illustrate a heavily loaded polymer blend, two materials of very different particle sizes are blended with a polymer surrogate. This footage documents the nature of the material blending and integration into a heavily loaded (~85%) polymer based paste in just over 2 minutes. The use of RAM™ technology is ideally suited for loading of solids into polymers and mixing to a high rate of dispersion and consistent viscosity throughout the blend.
Get a FREE ResonantAcoustic® Mixing Demo
We can schedule an on-site or online video demonstration with a LabRAM I or II (bench scale) mixer to show you the incredible versatility of RAM high viscosity mixing technology. We can mix any materials you wish to test, and we love challenging mixes!
- Mix 10x to 100x faster
- Eliminate cleanup & cross contamination
- Exceptionally thorough and consistent mixing
- Only available through Resodyn