Introducing the Award-Winning Industrial Mixer that Utilizes Sound Energy to Mix up to 100x Faster and More Uniformly than Any Other Mixer on the Planet
Bladeless ResonantAcoustic® Mixing (RAM) technology is proving itself integral to groundbreaking 3D printing designs, materials, and processes with its INCREDIBLE speed, power and reliable repeatability.
Resodyn Acoustic Mixers, Inc. offers the best-in-class industrial mixers for 3D printing of materials, including:
- Alloys
- Ceramics
- Plastics
- Polymers
- Powder Metals
- Powder Metal Coatings
- Resins
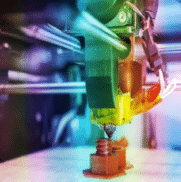
In 3D printing RAM Mixing technology facilitates accelerated reaction times and homogenization processes to achieve superior flow properties for powders, enabling printing of complex geometries.
- Increased dispersion rates, rapid emulsification and extended life suspensions promote efficiency.
- Reclamation can easily be attained without the need for additional equipment.
- Waste is significantly reduced and cycle time decreased, for improved production economics.
BREAKTHROUGH AT NASA
USING RESONANTACOUSTIC® MIXERS
NASA recently used ResonantAcoustic® Mixing (RAM) technology to invent GRX-810, a new 3D printed super alloy, which demonstrates exceptional durability and strength. GRX-810 is made by coating NiCoCr metal alloy powder with a film of nanoscale Y2O3 oxide articles using ResonantAcoustic® Mixing (RAM) technology. GRX-810 withstands temperatures exceeding 2000 ⁰F and lasts up to 2500 times longer than traditional alloys!
GRX-810 can be used in space launch systems, heat exchangers in nuclear power plants and other extreme temperature environments, thanks to RAM technology.
HOW RESONANTACOUSTIC® MIXING (RAM) WORKS
RAM Technology employs the power of acoustic waves to create intense vibrations within a vessel holding the substances to be mixed.
These vibrations generate localized pressure fluctuations and induce a phenomenon known as acoustic mixing. This process agitates materials at a particle level due to alternating pressure waves which break apart agglomerates, disperse particles and liquids causing rapid material dispersion, consistently resulting in a homogenous mixture.
- Uses vibration to send sound waves through the mix creating a much higher quality mix.
- Utilizes sound energy instead of force to mix much faster and much more uniformly.
- Reduces the mixing time from hours down to minutes.
- ResonantAcoustic Mixers shine where conventional mixing systems begin to fail.
INDUSTRY EXPERT
TESTIMONIALS
“... [ResonantAcoustic® mixing] is a fantastic technology. It has revolutionized the way we mix for development of materials for 3D printing...”
- Nik Ninos, Research and Development Manager, Calix Ceramic Solutions
“…The LabRAM II has yielded some surprising and exciting results for us. We actually made a new metal alloy for additive manufacturing...”
- Research Scientist, U.S Government Agency
“… We were using reciprocal shakers to dissolve product we sampled off one of our production lines, and it was taking four hours just to prep the material for testing. Once we started using the LabRAM, it cut that time from four hours down to 20 minutes...”
- Lab Supervisor, U.S. Polymer Products Company
THE UNIVERSAL
MIXING SOLUTION
The one-of-a-kind ResonantAcoustic® Mixer (RAM) product line harnesses the power of resonance (low-frequency sound) to generate powerful and efficient mixing of complex Solid-Solid, Solid-Liquid, Liquid-Gas, and Liquid-Liquid Blends. Making it the perfect industrial mixer for 3D printing, benefits include:
- 10-100X faster mixing times
- Bladeless non-contact mixing
- Consistent homogenization
- Mix using 1g up to 100g's of acceleration
- Highly reliable repeatability
- Simple straightforward scalability
- Erase cross contamination concerns
- Eliminate cleaning
- Easy to operate
- Massive cost saving
- Eco-friendly operation
- Unmatched safety
ADDITIVE MANUFACTURING
MIXING WITH SOUND ENERGY
Videos
Industry Folio
Dissimilar Powder Mixing
Dry ingredients can be difficult to thoroughly and consistently mix, particularly when the particles are of different sizes and characteristics. To illustrate effective and rapid mixing, 10 grams of fumed silica is blended with 100 grams of sand. Completed specimens exhibit no airborne fumed silica, demonstrating uniform blending at an order of magnitude difference in particle size.
Milling and Nano Coating
Coating larger particles with smaller ones is a common processing application, and milling is often a part of the same process. In this video, agglomerated carbon black particles are simultaneously milled to nano size particles that coat the plastic pellets completely in just a few seconds. The high speed video clearly illustrates the dispersion of carbon black particles, their de-agglomeration, and progressive and comprehensive coating of the plastic pellets.
Three types of materials account for most of what is used in industrial additive manufacturing: polymers, ceramics and metals. While polymers are the most commonly used, certain additive techniques make use of specific materials as well as the unique capabilities of RAM technology. These materials are most often produced in either powder form or as wire feedstock.
Download this folio of insightful testimonials and links to informative technical papers, articles and patents involving RAM’s impact on the development and use of additive manufacturing materials.
RESONANT ACOUSTIC MIXING (RAM) PRODUCTS
ADDITIVE MANUFACTURING MIXERS
Frequently Asked Questions
Q. What makes RAM special as it regards industrial mixing equipment for 3D Printing technologies?
A. Conventional industrial mixers have many drawbacks. These bladed systems struggle with achieving consistent results for materials with varying viscosities and/or particle sizes. The mechanical action of the blades can create excessive shear forces and generate local shear forces that can increase temperatures which can degrade sensitive materials. High shear forces can alter material properties. RAM’s patented mixing process is bladeless and effectively rectifies the deficiencies posed by conventional mixing systems. The benefits of RAM include, but are not limited to dramatically improved mixing times, shear force reduction, minimal overheating of mixed materials, consistent product homogenization, and repeatable results from mix to mix.
Q. Where has RAM been successfully implemented for additive manufacturing?
A. ResonantAcoustic® Mixing technology has been accepted and utilized worldwide in over 40 countries for a broad range of industrial applications. Additive manufacturing mixers are a must have technology for most 3D printing firms.
Q. What industries does RAM service?
A. Greater than 20 distinct industry markets have adopted RAM technology as a standard industrial mixing - processing practice. Each industry has specific requirements with countless individual applications. Primary industries for Resodyn Acoustic Mixers, Inc. include:
- Energetic Materials (munitions, propellants, explosives, and pyrotechnics)
- Pharmaceutical Products
- Energy Storage/Battery Material Processing
- Chemical Production
- Adhesives & Sealants (Aerospace and Defense)
- R & D Services
- Highly Viscous Materials
- Specialty Products The company actively services other applicable market areas but believes that its overall success is best served by concentrating on its primary markets.
Q. What materials can be mixed?
A. The RAM product line is designed to mix virtually any combination of materials. The technology truly begins to shine where conventional (bladed) mixing systems begin to faulter or altogether fail.
Q. What types of materials does Ram successfully mix?
A. ResonantAcoustic® Mixers deliver a universal platform which produces repeatable results for any combination of solids, liquids, and gases. RAM is extremely well suited for the challenge of highly viscous materials. RAM successes include deagglomeration, sieving, and coating.
Q. What sizes are available?
A. ResonantAcoustic® Mixers range in size from bench scale batch production models - LabRAM I (500g payload capacity) to production scale batch models - RAM 55 (420 kg payload capacity). Resodyn’s Continuous Acoustic Mixer creates ongoing production capacity of up to thousands of kg/hour.
TRUSTED BY
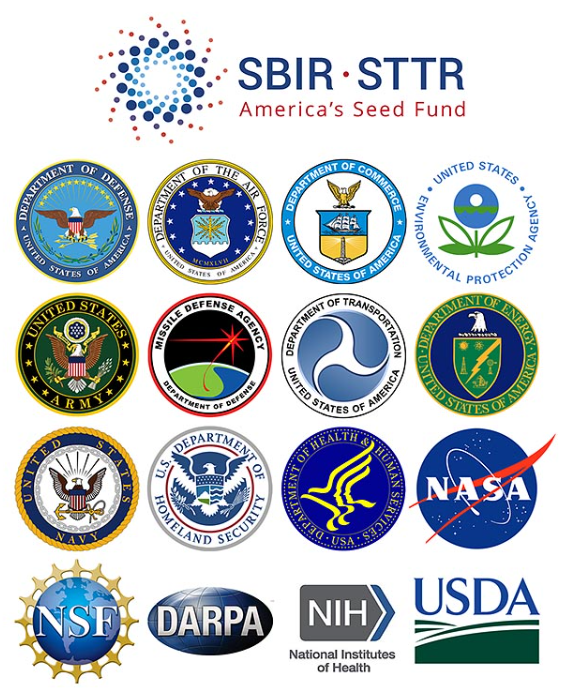